Last updated on
Prefab houses are more durable than stick-built homes. We will prove the case in this article. Read on!
Actually, we’re going as far as to say that stick-built homes are not as sturdy as traditional-style manufactured houses. With the exception of mobile homes, the components that are nailed in place on a stick-built construction, are glued and nailed in the manufacturing process. That is, the components are assembled in a perfect environment.
Studs must be straight, or the systems of production won’t work. Everything is put together in a way that makes them straight and consistent. Pre-installed plumbing and electrical can be attached easily. There is some finishing work on the inside that can be done in a day. The end product is actually stronger and tighter than a stick-built from the ground up.
Of course, the design, materials, and company that builds the modules all affect the home’s long-term resilience. Sometimes homes are advertised as disaster-resistant, but whether or not a structure can be lived in after is up for question. Many homes are designed to do more than survive natural disasters.
Durability is one of the key factors that make prefab homes worth it and help maintain their value.
Why Prefab Homes are Durable
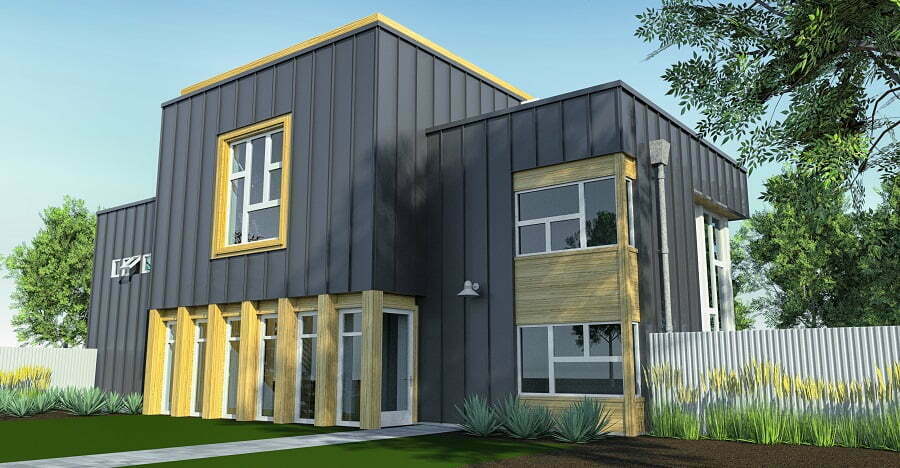
Prefabs have been around for decades now, so they’ve had plenty of time to develop. In fact, some prefabricated houses were built before World War II. That’s because many companies began building these structures during the Great Depression when demand was low. As the economy improved, however, demand increased, which led to an increase in production.
Today, most prefabrication takes place at factories where skilled workers assemble modular components. The factory also provides quality control measures such as inspections and testing. This ensures that each component meets its specifications. It is an industry that’s rapidly changing and improving.
When it comes to durability, there are two main factors: construction methods and material selection.
Construction Methods
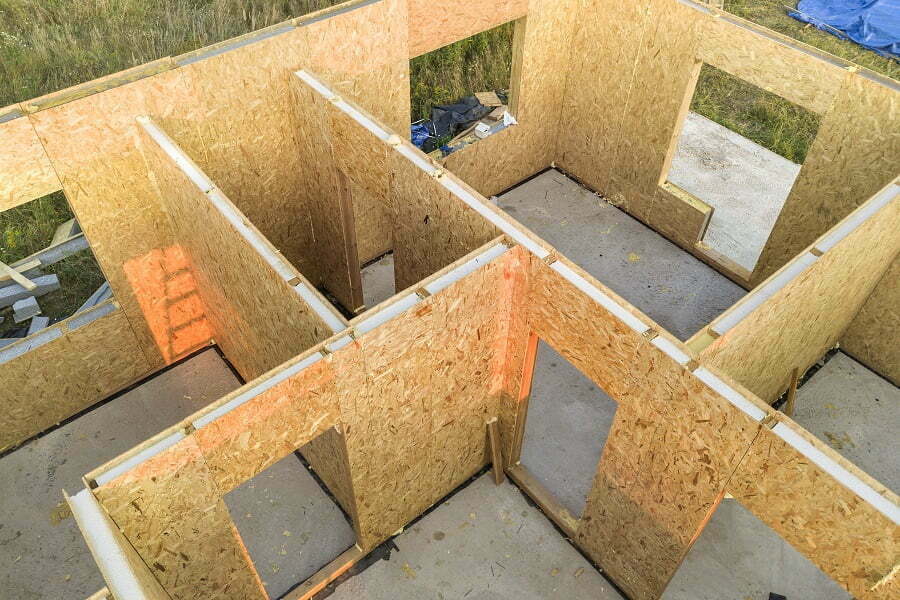
There are three primary ways to construct buildings today: prefab panels, stick frame, steel framing, and concrete block. Stick frames consist of wood beams with wooden planks nailed onto them. Steel framing uses metal rods instead of wood. Concrete blocks use cement bricks stacked together without any other support system.
Each method has advantages and disadvantages. For example, concrete blocks are strong and easy to build, while steel framing requires less labor and allows you to customize your walls.
However, both types require lots of maintenance over their lifetime. If you’re looking for something that will last longer, consider using one of the following options.
Steel Framing
Steel framing is typically used for larger projects like commercial buildings. It consists of large structural members made from either galvanized steel or stainless steel. These pieces connect into a grid pattern that supports roof trusses and floors. They come preassembled and ready to install. Because this type of framing is heavy-duty, it usually needs additional reinforcement. You’ll need to hire professionals who specialize in installing steel framing systems.
Stick Frame Construction
Stick frame construction is often found in smaller residential properties. It involves connecting individual 2x4s boards with nails or screws. While this may seem simple enough, it does take skill and experience to ensure that everything fits properly. Additionally, if you want to add insulation between the studs, you must drill holes through every board. Finally, since this style doesn’t provide much strength, you should only use it for small projects.
Concrete Block Building
Concrete block construction is probably best known for being used in cinder block homes. But it can be applied to almost anything. Blocks are available in different sizes, shapes, colors, textures, and finishes. Some people prefer natural-looking materials, but others enjoy more modern designs. Regardless of what kind of look you choose, concrete block construction offers several benefits. First, it’s extremely affordable. Second, it’s very versatile. Third, it’s highly customizable. And finally, it’s relatively quick and easy to construct.
Selection of Materials
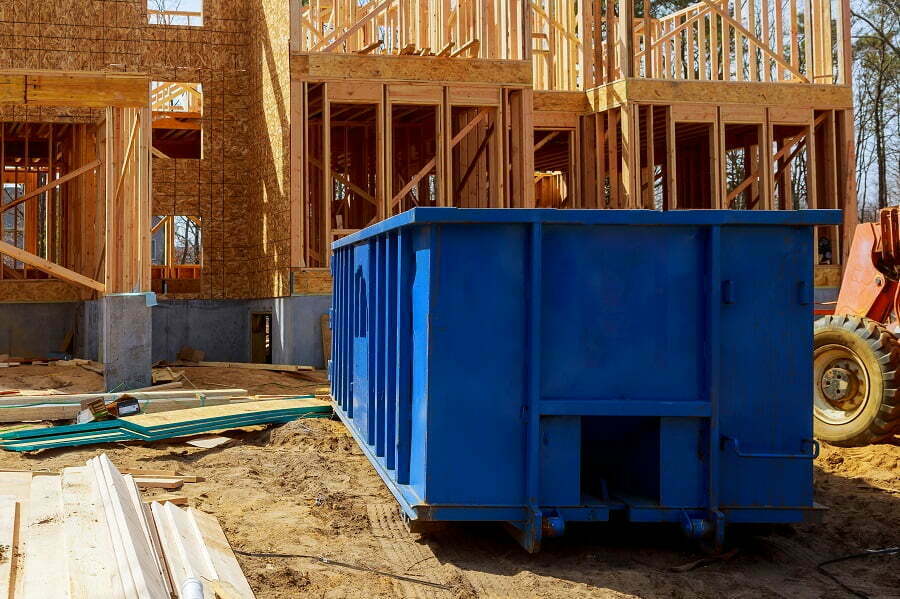
The second factor affecting how long a prefab home lasts is the choice of materials. There are four common choices: vinyl siding, fiberglass exterior cladding, aluminum windows, and composite decking.
Vinyl Siding
Most homeowners opt for vinyl siding because it looks great on nearly all kinds of property. Plus, it’s inexpensive compared to other alternatives. Unfortunately, vinyl siding isn’t particularly durable. Over time, it tends to crack and peel away from the wall. This makes it susceptible to water damage.
Fiberglass Exterior Cladding
Fiberglass exterior cladding provides an attractive alternative to vinyl siding. Like vinyl, it comes in many styles and colors. Unlike vinyl, however, it won’t fade when exposed to sunlight.
Aluminum Windows
Many builders recommend replacing old windows with energy-efficient models. The most popular option is aluminum. Not only do they have better-insulating qualities than traditional glass, but they also cost significantly less.
Composite Decking
Another material commonly installed over wood decks is composite decking. It has similar characteristics as hardwood flooring, including resistance to moisture and rot. However, unlike real wood, it requires little maintenance.
Roof Types
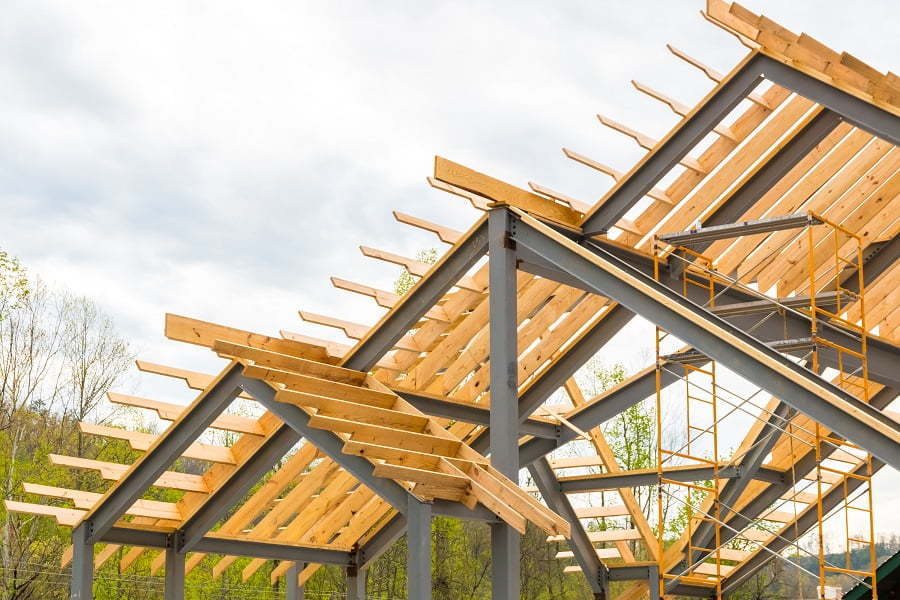
There are two main types of roofs: flat and pitched. Flat roofs don’t slope at all; instead, they’re completely level. Pitched roofs gradually rise toward their peak. Both options offer advantages and disadvantages. For example, flat roofs tend to leak easily. They require additional waterproofing measures such as flashing and caulking. On the flip side, flat roof systems are easier to install and maintain.
Pitch roofs come in three basic forms: gable, hip, and gambrel.
Gables are steeply sloped roofs that resemble those seen on barn homes. Hip roofs feature a gentle pitch that resembles a human backside.
Gambrel roofs are slightly steeper than hips, making them ideal for larger buildings like churches. All three varieties provide excellent insulation properties. In fact, some experts claim that pitched roofs actually reduce heating costs by up to 20 percent.
Gambrel roofs are often preferred because they allow for greater interior space. A typical gambrel roof features a ridge beam running along its centerline. Atop this beam sits a series of rafters spaced evenly apart. These rafters support a layer of sheathing or plywood covering. Finally, there’s another layer of shingle or tile covering.
Solar panels: Solar power is becoming increasingly important around the world. As solar technology improves, so does our ability to harness the sun’s rays. Today, we use photovoltaic cells to convert light into electricity. Photovoltaics work much like batteries—they store electrical charges. When the sun shines, these devices absorb the energy and release electrons. If you want your own source of clean renewable energy, consider installing solar panels on your home.
Each piece of roofing adds strength and durability.
Siding Options
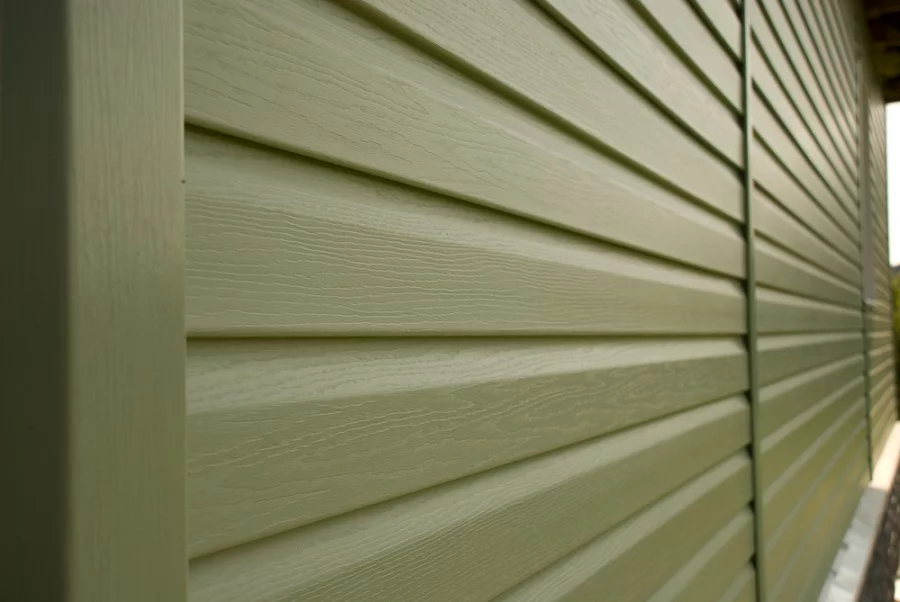
When choosing your building materials, consider these factors: appearance, ease of installation, longevity, and affordability.
- Appearance – When selecting siding, think about whether you want something that blends into the environment or stands out against it.
- Ease of Installation – If you plan to build yourself, make sure the type of siding you select will fit through standard doorways and around corners without requiring special tools.
- Longevity – Consider what kind of weather conditions your area experiences. Will you be living in a place where snow falls regularly? Or does rain wash off the paint quickly?
- Affordability – Make sure the price tag fits within your budget. You can always add more later if necessary.
Comparing Prefab Homes to Traditional Building
Precision: Jigs and guides can be used to cut more precisely. It is possible to cut sheetrock and plywood. It reduces the number of materials wasted.
Joining: It is possible to join individual pieces in a factory. Pre-drilled and joined critical wood framing pieces help them hold better.
Cost: Factory-built homes cost significantly less than traditional construction methods. This means lower prices for consumers.
Quality: Quality assurance checks ensure that each home meets quality standards before leaving the factory.
Safety: Safety precautions are taken during manufacturing. Workers wear safety equipment and follow strict guidelines.
Efficiency: Manufacturing takes advantage of modern technology. Computerized machines do most of the work while humans oversee operations.
Environmental Impact: There is no waste from cutting lumber, transporting raw material, or disposing of debris. Less energy is needed to manufacture products.
Control: The inside of a factory allows for greater control over the build. The glue or seal is not interrupted by rain or snow and can dry itself out.
Oversight: The general contractor and the designer are in charge of every step of the building process, which makes it less likely that workers will misinterpret plans, miscommunicate, or take shortcuts.
The durability of the finished home is affected by these small details. A piece of wood that is too short leaves room for movement during a strong wind. Excess stress and unusual loads can be put on surrounding boards by a board that is too long. Improperly applied seals can allow air and water to enter, leading to the decay of wood. The control of the factory environment can lead to a home with a level of fit, finish, and durability that far surpasses traditional building methods.
Comparing Prefab Homes to Mobile Homes
There are doubts about the strength of mobile manufactured homes. Mobile homes have their own laws and market segments, which affect their durability. They also require different types of foundations.
Mobile homes are not always anchored to a foundation. They are built using lightweight steel framing or wood platform on wheels. This makes them vulnerable to being knocked over in high winds. In addition, they may tip over when hit by heavy objects such as trees or cars.
They are usually placed on concrete slabs rather than soil. Concrete has low tensile strength compared to soil. Soil provides support for weight-bearing walls. Slabs provide stability but cannot bear much weight.
A mobile home’s location affects its ability to withstand extreme temperatures. Most mobile homes are located near bodies of water because this helps keep them cool. However, some areas experience scorching summers. These locations must use more insulation to prevent heat loss.
In contrast, manufactured homes are typically attached to permanent foundations. Manufactured homes are often set into the ground like any other structure. Their frames are made of metal beams and columns instead of wooden planks. Metal supports make manufactured homes stronger than mobile homes.
Manufactured homes are designed to last longer than mobile homes. Many manufacturers offer warranties ranging from 20 years to 50 years. Some even guarantee lifetime serviceability.
These guarantees come at a price. Manufacturers generally cost more per square foot than mobile home builders. But they produce higher quality structures.
The Factors of Durability
The following are the factors that impact the durability of prefab homes and prefab additions the most.
Transportation and Assembly: The Prefab home modules must be built strong enough to make the journey from the factory to the construction site intact and be lifted into place with cranes. The module’s strength is what makes a finished home reliable.
Installation: Once installed, the pre-built components need to remain stable until the completion of the interior finishes. If problems are installing the modules, then the entire project could fail.
Interior Finishes: Interior finishing touches add value to the home. When done correctly, it will increase the longevity of the home.
Weather Resistance: Weather resistance refers to how well the exterior materials resist damage caused by weather conditions. For example, if you live in an area where snow falls regularly, your roof should be constructed not to leak. Similarly, hurricane shutters should protect windows and doors if you live in a region prone to hurricanes.
Fire Safety: Fire safety means making sure that fire can’t spread through the building. A properly insulated wall between rooms prevents smoke from spreading throughout the home. Windows and doors should all open outwardly to allow airflow.
Energy Efficiency: Energy efficiency refers to keeping energy costs down. Insulation keeps out cold during winter months while allowing warm air inside during summer. Proper sealing around windows and doors reduces drafts.
Security: Security includes protection against intruders. Doors and windows should have locks or bars. Locks may also include deadbolts.
FAQ
Prefab houses usually last 30 to 40 years before needing major repairs. They tend to require less maintenance over time as compared to traditional stick-frame buildings. This is due to their modular design, which allows easy access to each component.
Costs vary depending on size, style, and options selected. Prices range from $20,000 to $100,000.
Yes! You can use prefabrication kits to create a custom home. Kits provide everything needed to complete a project, including foundation, walls, flooring, plumbing fixtures, electrical wiring, insulation, cabinets, countertops, appliances, etc. Kit prices start at about $10,000.
Many homeowners find them attractive when placed next to other housing types such as single-family homes, townhouses, apartments, condos, cottages, and even barns. Some prefer them because they offer privacy and security. Others like the fact that they are easier to maintain.
Yes. All manufactured homes meet current standards set forth by the Department of Housing & Urban Development. Manufactured homes must pass rigorous inspections for structural integrity, health and sanitation, accessibility, and durability. The National Institute of Building Sciences has certified more than 1 million manufactured homes since its inception in 1989.
It depends on what type of kit you choose. Prefabricated homes typically take anywhere from 6 weeks to 3 months to construct. Most manufacturers ship completed units directly to job sites.
Table of Contents