Last updated on
The prefab industry continues to grow, with more people choosing modular homes over traditional stick-built houses. These are all trends of the industry in 2022.
The reasons are many: affordability, flexibility, customization, energy efficiency, durability, design freedom, and the ability to build a home that fits your lifestyle.
If you want to learn about some of the most popular prefab market trends today, keep reading!
More Affordable Housing Options
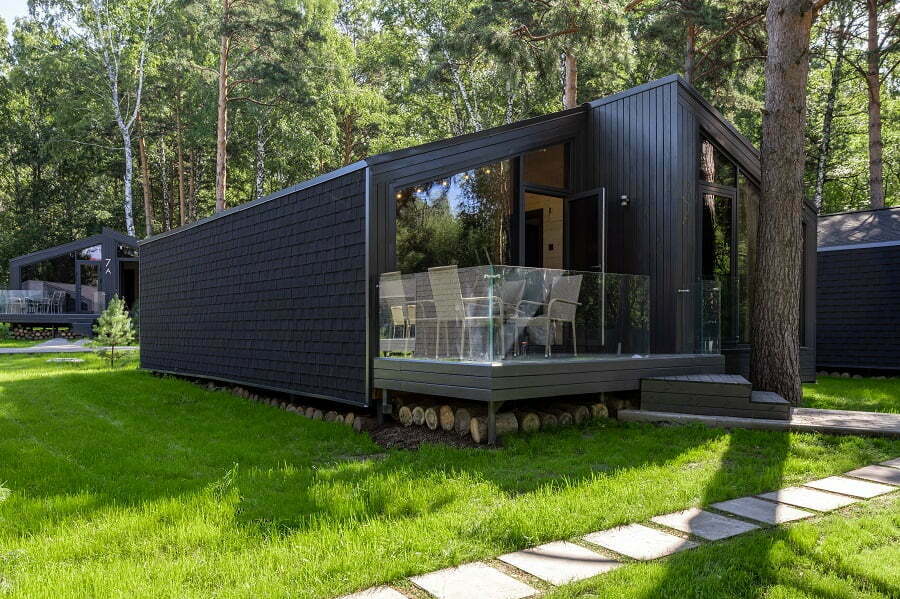
As we mentioned above, affordable housing is at a premium right now. That means if you don’t have enough money saved up or can’t qualify for financing through conventional lenders, it may make sense to consider a prefabricated option.
These days, builders offer several different types of prefab options, including manufactured homes, which come factory-built; panelized construction, where sections of walls and roof panels are preassembled offsite and then shipped to the job site; and modular homes, which are constructed using standardized modules that fit together like Lego blocks. Each type has its advantages and disadvantages, so read our article here to find out what’s best for you.
Flexibility and Customization
If you’re looking for something unique but not too expensive, a custom home could be just what you need. However, when you buy a custom home, you’ll typically pay thousands extra than someone who buys a standard model.
With prefabrication, however, you get all the benefits of a custom home without having to spend as much time and effort designing and planning each room. You can customize everything from floor plans to appliances to paint colors. And because manufacturers make prefab homes rather than individual contractors, they tend to cost less than custom builds. On top of that, you can always order prefab additions and even add a second floor down the road to extend your house.
Energy Efficiency
Energy efficiency isn’t always a top priority during the initial stages of homebuilding, but once you’ve moved into your new place, you’ll quickly realize how important this factor is. In fact, according to the U.S. Department of Energy, “energy-efficient buildings use 20% fewer resources per square foot compared to non-efficient buildings.”
So if you’re thinking about going green, look no further than prefabrication. Manufactured homes are already highly energy-efficient, while modular homes often feature high insulation levels and other features designed specifically to reduce heating and cooling costs. Together with smart home technologies, these make prefabs more and more attractive.
Increasing Durability
Manufactured homes aren’t only great for saving space and cutting down on construction costs–they’re also highly durable. Unlike their stick-built counterparts, manufactured homes are usually built with thicker materials and more robust framing systems. This makes them far better able to withstand extreme weather conditions such as hurricanes and tornadoes. They’re also generally easier to repair in case of damage.
Design Freedom
Another benefit of prefabricating your next home is that you won’t feel limited by any preconceived notions of what a particular style should look like. Instead, you can choose exactly what kind of interior finishes you’d like and even pick specific designs for certain rooms. If you want to go big, there are plenty of ways to do that, whether it’s adding an open concept layout or building a sprawling ranch house. The possibilities are endless!
Increasing Convenience
Prefabrication offers many conveniences over traditional methods of constructing a home. For starters, most models include plumbing fixtures, electrical outlets, windows, doors, etc., making installation faster and more convenient. Plus, since these houses are built by factories instead of individual contractors, you can save yourself some hassle along the way.
Better Quality Control
When you build a home from scratch, you know every aspect of the process will be done correctly. But when you purchase a prefabricated home, you still receive quality control measures throughout the entire manufacturing process. Manufactured homes undergo rigorous testing procedures to ensure they meet industry standards, from design approval to final inspection before delivery.
More Customization Options
One of the most significant advantages of buying a prefabricated house is that you have complete freedom to make changes whenever you see fit. Whether you decide to add additional rooms later on or change one bathroom for another, you don’t have to worry about getting permission first. All you have to do is contact the manufacturer and let them know what modifications you’d like to make. Then, they’ll send you a quote detailing the price of those upgrades. Once you approve the cost, they’ll begin work immediately.
More Flexibility
The last advantage of purchasing a prefabricated manufactured home is its flexibility. You may not think much about it now, but having the ability to customize your home at any time could come in handy someday. Maybe you find out after moving in that you need a more oversized kitchen, or maybe you get tired of living in the same room arrangement day in and day out. Whatever the reason, if you buy a prefabricated model, you can easily modify it without worrying about breaking the bank.
Bigger Cost Savings
The best part? Prefabricated homes typically offer lower prices than other types of housing options. In fact, according to HomeAdvisor, the average cost per square foot of a modular home ranges between $100-$200. That means you’re saving money right off the bat. And because manufacturers often pass savings onto buyers, you can expect to pay even less once you factor in all the extras included with each unit.
Prefab and Modular Home Construction Trends
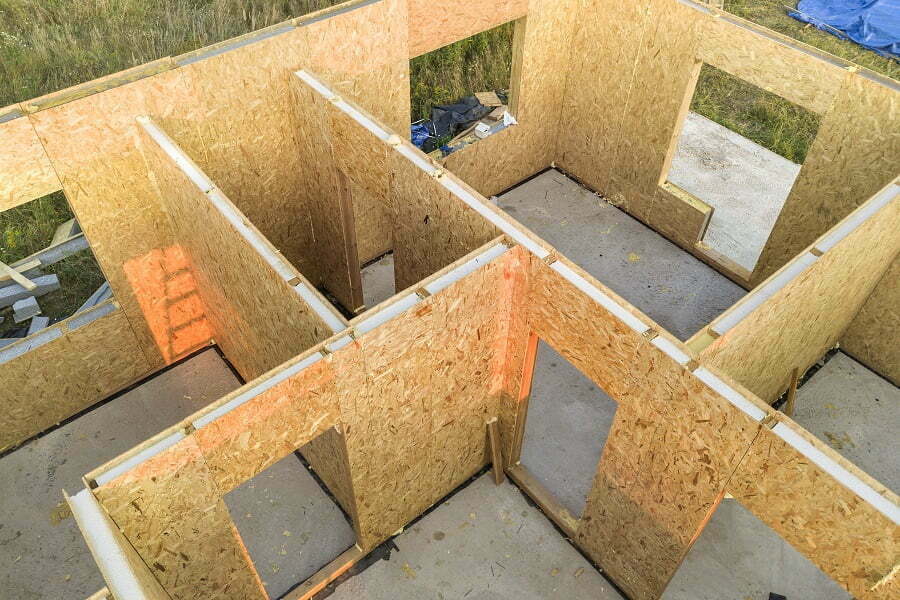
The most common types of prefabs include:
Kit houses – These are smaller versions of traditional stick-built homes. They’re typically used for vacation properties, second homes, or other small spaces where space is limited. The kits come preassembled and ready to move into place.
Panelized buildings – Similar to kit houses but larger, these panels are assembled offsite and brought together piecemeal before installation. This type of building is perfect for large families who want plenty of space while maintaining an affordable budget.
Manufactured log cabins – Made chiefly of wood, this cabin style has been around for centuries. It’s also known as “stick frame” construction because logs are stacked together to form walls. While there are several different styles available today, the basic structure remains the same.
The Prefab Industry is Growing
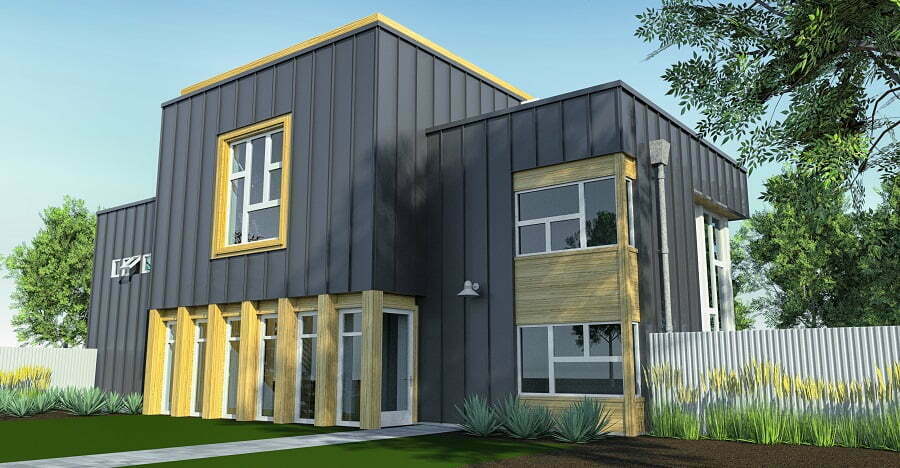
The building industry is starting to realize the full potential of building homes in a factory, which is why prefabricated & modular construction is growing.
According to a report by Global Industry Analysts Inc., the global market for prefab and modular buildings will reach $153.7 Billion by 2026. The growth was driven primarily by increased demand for energy-efficient housing solutions that are cost-effective and can be delivered quickly. In addition, they have found that manufacturers have increased their profit margins due to lower material costs and reduced labor requirements.
Manufacturers are increasingly using advanced technology such as 3D printing to reduce production times and improve quality control. For example, one manufacturer uses robotic arms to assemble roof trusses on-site instead of relying solely on manual labor. Another company offers a fully automated manufacturing process that allows customers to choose from hundreds of designs online.
Table of Contents