Last updated on
Prefab homes have a long history that dates back to the 19th century. Though it is only now becoming prevalent in home construction.
Few people know that the first prefab home was designed in the early 19th century. Or that manufactured homes have saved families who have lost their homes during WWII. They have a long history, and we can still find old prefab homes worldwide that tell a story.
Let’s go on a journey to see how prefab homes have evolved from temporary housing to sustainable dream homes of today.
Early History of Prefab Homes
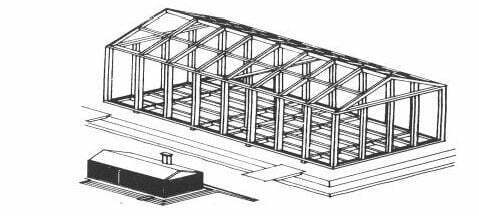
The history of prefab homes, i.e., houses built in one place, then transported and reassembled in another, go back a rather long time. Many believe “Manning Portable Cottage” to be the first advertised prefab home, conceived and designed in 1830 by H. John Manning, a London carpenter.
However, the idea of manufacturing prefab homes in relatively large batches was introduced around the mid-19th century during the Gold Rush period in the United States. The quick construction time of these houses made them popular with the California prospectors and prefabricated homes retained their popularity in the US right through to the first half of the 20th century.
Back then, these were known variously as kit houses, mail order homes, ready-cut or pre-cut houses, or catalog homes. From simple bungalows to two-story houses to imposing mansions, the manufacturers offered a wide range of styles and plans.
Sears, Roebuck, and Company was the leading manufacturer of kit houses from this period. During its 32-year involvement with prefab homes (the company closed its prefab department in 1940), Sears offered as many as 370 proprietary designs in their ready-to-assemble catalog homes.
Modular Housing Schemes (1920s-30s)
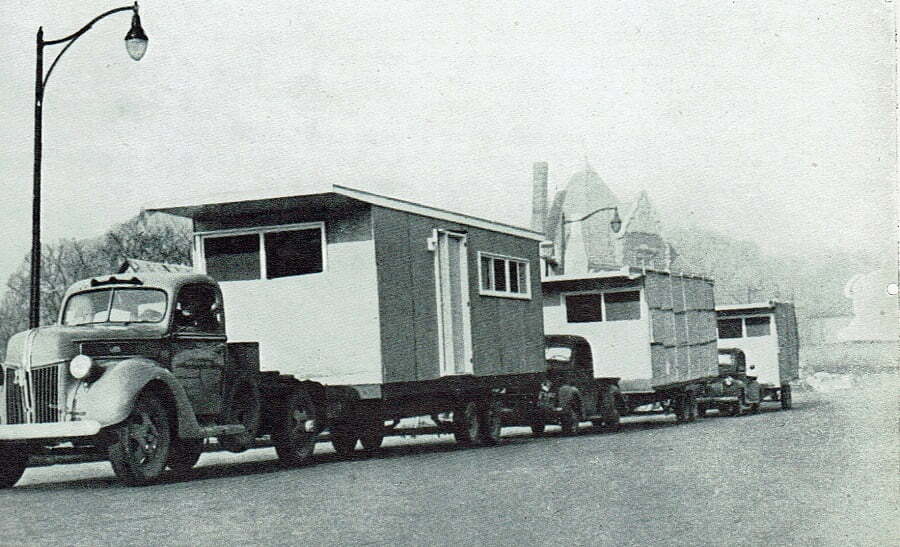
Although prefabricated construction and modular construction overlap in certain aspects, the key difference between the two is that a modular home is typically built in large sections, such as roof panels, trusses, entire walls with pre-fit windows, etc.
In the US, the noted engineer-architect Buckminster Fuller is credited with the first modular housing schemes. His Dymaxion House, built following a modular construction design, included advanced prefab features such as complete bathroom modules. Fuller’s ideas were, however, never fully realized since he left Dymaxion Company shortly after coming up with his modular home design and moved on to other projects.
Still, the practicality and convenience of Fuller’s modular housing schemes meant that they were used by the US military during WWII when the modules were shipped to US military bases overseas.
Prefab Homes Postwar (Housing Crisis)
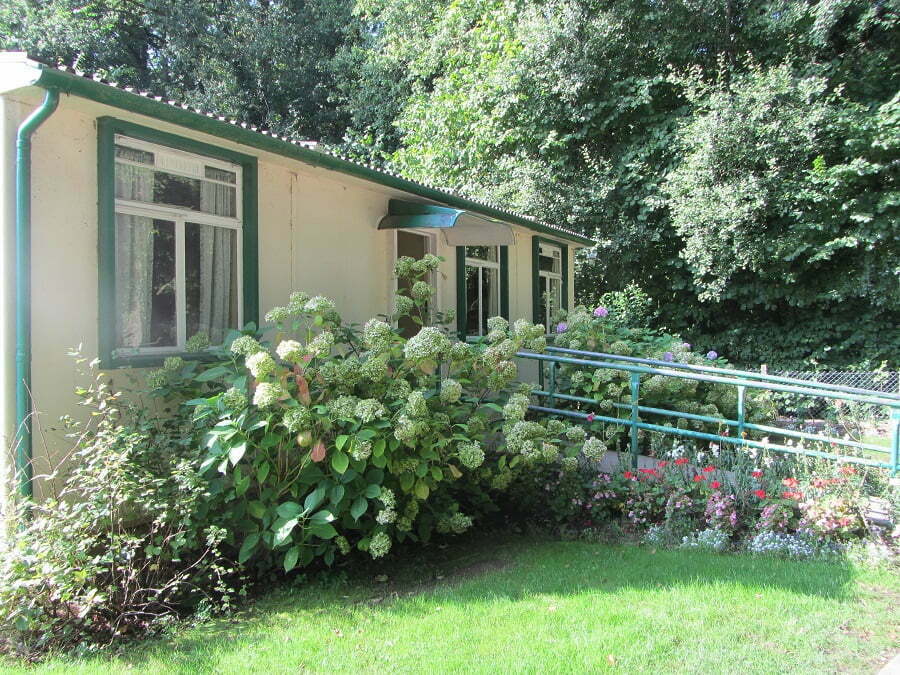
Modular and prefab homes saw a noted resurgence in production in the postwar era. However, this time, it was mostly to address the housing shortage problem that made temporary or “stopgap housing” an urgent necessity.
But, unlike the variety and innovation offered by Sears kit houses or by Fuller’s designs, the new construction method was largely homogenous in style and was adopted for mass residential housing. Steel, aluminum, and plastics replaced wood as primary materials for these mass-scale housing projects. In most cases, the quality of the construction was poor (fragile walls, etc.), and residents chose to live in these homes only out of sheer necessity.
Although modular home constructions of today bear little resemblance to these cheap factory-built houses of yore, the poor quality of the latter has led to a stigma against modular homes (and to prefab construction in general) that persists to this day.
Bungalows and Prefabricated Kit Houses
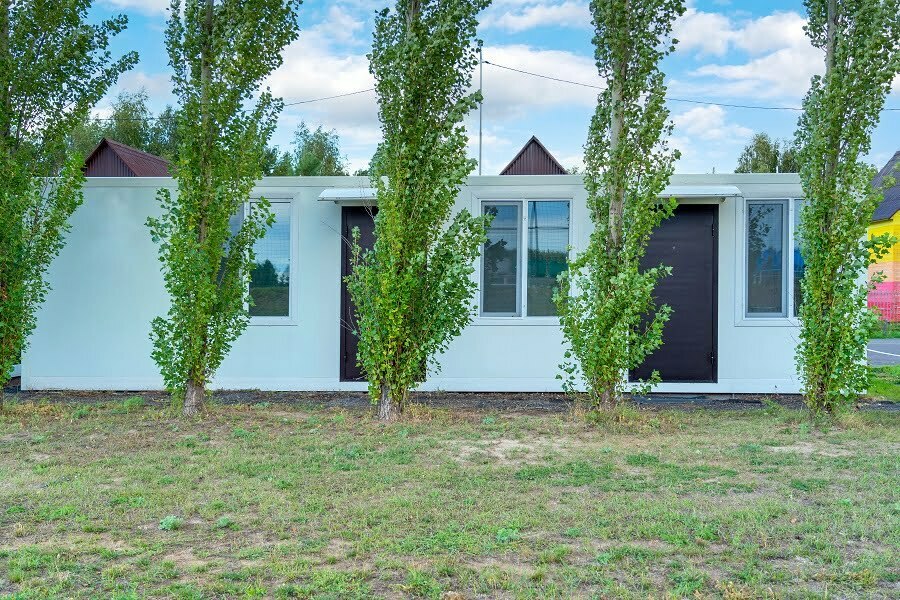
While these changes were taking place, many famous architects kept experimenting on their own designs and ideas of beautiful yet affordable prefabricated homes. These efforts’ most notable and sustained came from no less a famous architect than Frank Lloyd Wright.
For his American System-Built Homes (ASB) project, Wright designed as many as three dozen different housing models ranging from modest suburban homes to luxurious bungalows right up to grand colonial mansions.
Wright kept up his work on prefabricated kit houses with his “textile block” designs of the 1920s right through to his “Automatic” Usonian concrete modular homes introduced in the early 1950s. At about the same time, Marshall Erdman, once an assistant to Wright, introduced his own version of prefab homes, the “U-Form-It” prefab home kits, to the private residential construction market.
These innovative designs, even if not always commercially successful, played a major role in the evolution of prefab home construction during subsequent periods.
Modular and Mobile Homes
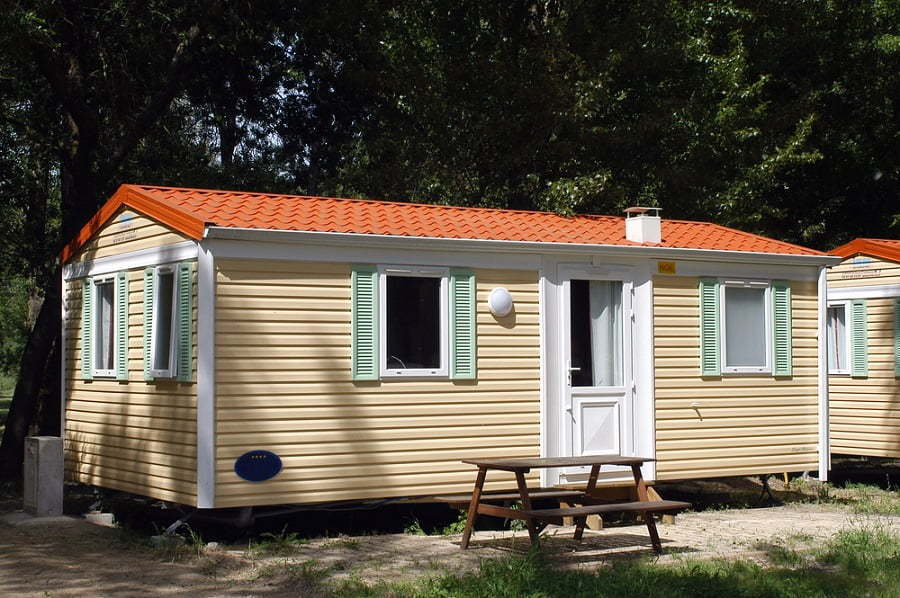
Mobile homes, still another form of prefabricated construction, have origins in ‘travel trailers’ or ‘trailer coaches.’ The automobile-pulled trailer coaches were introduced to the residential market in about 1926 and were marketed to individuals whose lifestyle required frequent mobility.
Later, during the 1950s, the concept of mobile homes merged with the large-scale modular home constructions discussed earlier. Although called mobile homes or temporary housing, these units were often permanently installed with a complete masonry foundation. If not, they were still left lying in a location for extended periods of time.
Subsequently, these housing complexes came to be referred to as ‘trailer parks’ with definite negative connotations attached to them.
However, mobile homes of today are significantly different both from modular homes and from travel trailers or coaches.
Evolution of Prefab Home Designs
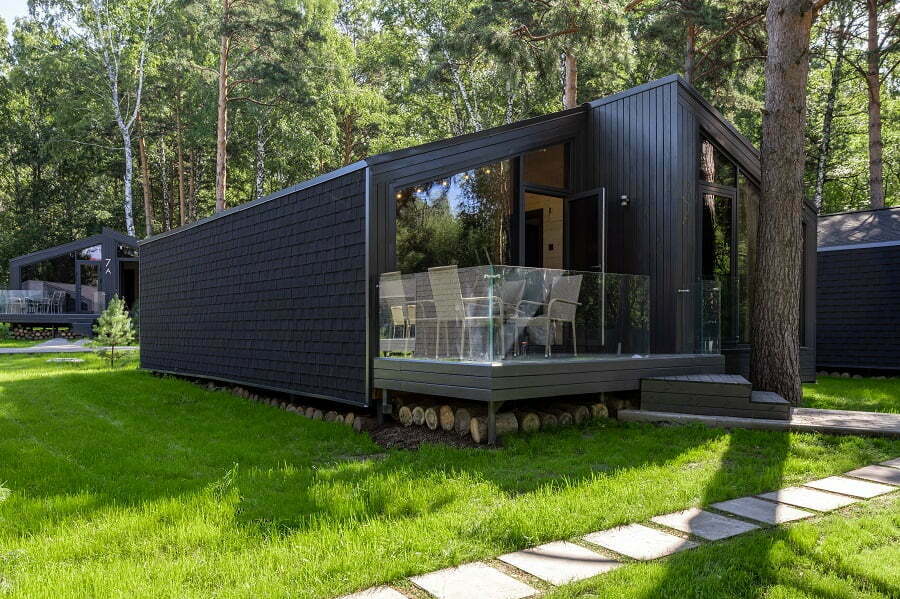
Over the decades, prefab home designs have been through various changes and those in various different directions. At present, broadly, three types of different prefabricated constructions are used for both residential home and commercial buildings.
These three subcategories of prefab homes, namely Modular, Volumetric, and Prefab Kit Homes, come with their own specific traits while at the same time offering a varied range of options in terms of style, models, construction, customization, and more.
For example, Klip Houses are designed following the modular architecture method, whereas the now well-known Container Housing projects mostly follow the concepts used in kit homes.
Prefabs and the Modernist Movement
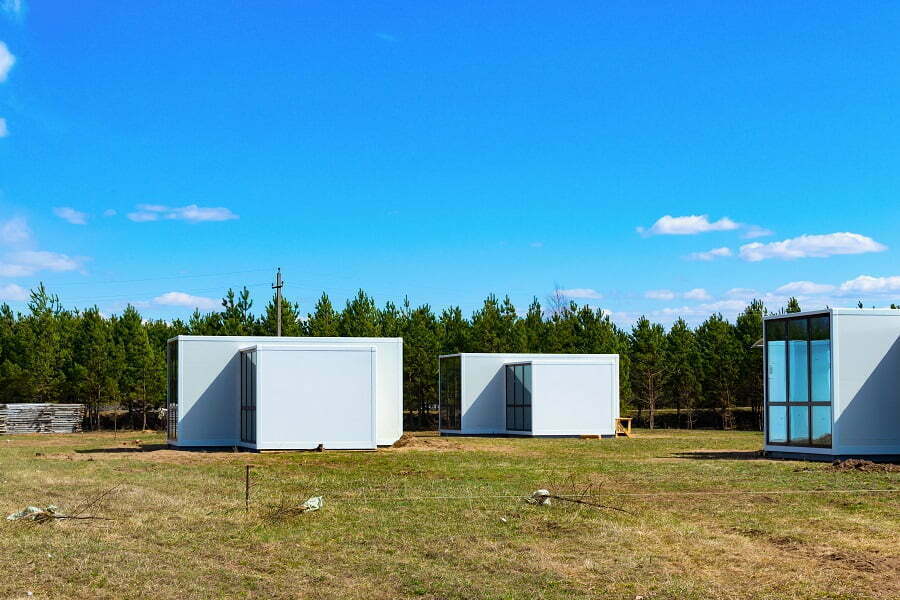
Many of the prefab designs that have become standardized today had their origins in the experimental and often revolutionary concepts conceived by many visionary architects whose works have been part of the modernist movement in architecture.
The list is too long to mention here, but a few works that merit special mention include:
- George Nelson’s futuristic designs and his forward-thinking solutions with regard to overpopulation by installing modular home units on a single mass-structural frame
- French architect Guy Dessauges’ fanciful and innovative prefab leisure house designs
- Moshe Safdie’s revolutionary prefab modular megastructure, Habitat 67
- The Nagakin Capsule Tower, built by the Japanese architect collective The Metabolists (the group is said to have a big influence on American architects, especially in relation to large-scale modular construction)
- Paul Rudolph’s Oriental Masonic Gardens project which has directly inspired the Container Housing/Container City projects.
Prefabricated Commercial Buildings
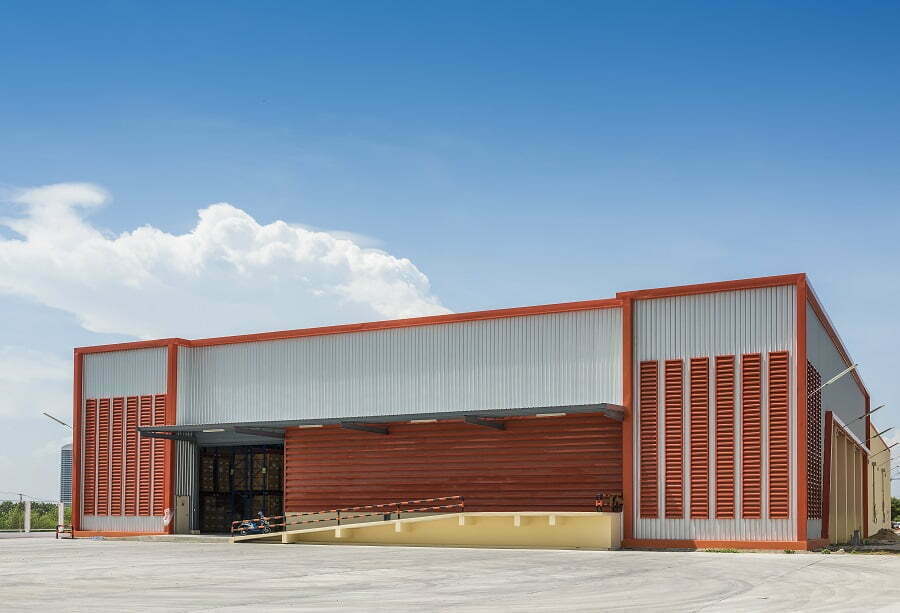
Although up until recent years, prefab home manufacturing catered largely to the residential sector, advances in technology have meant that an increasing number of commercial buildings (warehouses, offices, department stores, supermarkets, mega malls, and even larger constructions) are built using prefabrication techniques.
The prefab commercial buildings of today are relocatable, efficient, attractive, customizable, and extendable. The volumetric architecture mentioned earlier is most suitable for producing prefab commercial structures.
Is Prefab the Future of Construction?
Although this is still a somewhat contentious issue, many believe that the future of construction lies in a rush to prefab techniques. The reasons cited include:
- New manufacturing technologies such as 3D printing and additive manufacturing.
- Use of laser scanning technology for field verification.
- CNC-controlled technologies.
- Increasing use of robotics both on- and off-site.
A Case in point: The BSB (Broad Sustainable Building) headquarters in China, a 57-story tower the company had built in no more than 19 days already back in 2015! That equals a construction pace of 3 stories per day!
Table of Contents