Last updated on
Pratt homes prices are enticing because they blend affordability with the promise of sustainability and superior quality.
Pratt Homes offers a wide range of building and real-estate solutions specialized in sustainable design and comfort, and their prices stand testament to their dedication to quality, efficiency and affordability.
This is the perfect place if you’re interested in getting the in-depth information on Pratt Homes’ pricing dynamics.
Whether it’s about their modular homes or prefab homes, read on to find detailed discussions about the varying factors influencing the cost, the array of options in different price brackets, and how Pratt Homes ensures maximum value for your money.
The estimated price range for these homes is between $70 and $100 per square foot. These estimates are all-inclusive, covering the cost of the modular home, site work, assembly, and interior finishes, excluding the cost of land.
Pricing ranges:
- Ranch (1 Bedroom, 1 Bathroom, 399 Square Feet): $39,900
- Whitehouse (1 Bedroom, 1 Bathroom, 600 Square Feet): $58,670
- 1676 (3 Bedrooms, 2 Bathrooms, 1,160 Square Feet): $106,267
- Teresa (2 Bedrooms, 2 Bathrooms, 1,577 Square Feet): $137,218
- Jennifer (3 Bedrooms, 2 Bathrooms, 1,800 Square Feet): $152,196
- Georgetown (3 Bedrooms, 2 Bathrooms, 1,900 Square Feet): $158,557
- Sequoia (3 Bedrooms, 2 Bathrooms, 2,670 Square Feet): $200,147
- Goliath (4 Bedrooms, 3 Bathrooms, 3,120 Square Feet): $218,400
Key takeaways:
- Pratt Homes prices blend affordability with sustainability and quality.
- Average modular home cost ranges from $70 to $100 per sq ft.
- Factors influencing modular home prices include design complexity and region.
- Custom prefab home prices vary based on design, materials, and builder.
- Land, site prep, and foundation costs are important considerations.
Average Modular Home Cost
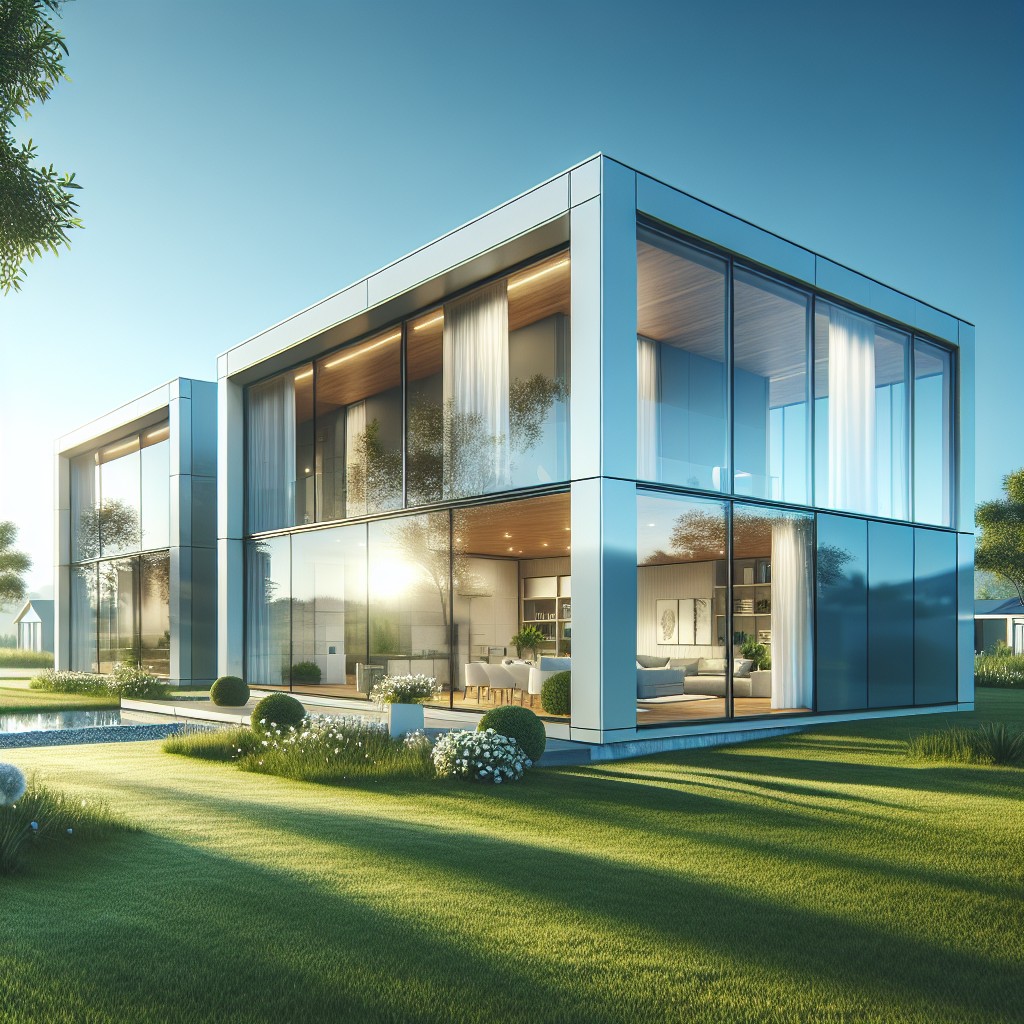
The average cost of modular homes can vary significantly based on factors like size, design, and location. Typically, prices range from $70 to $100 per square foot, with a medium-sized home being somewhere between 399 and 3,000 square feet. These costs usually include the basic structure but may not cover other necessary expenses such as land purchase, site preparation, and utility hookups.
To put this into perspective, consider these points:
- Smaller or simpler designs will be at the lower end of the cost spectrum, offering affordability without sacrificing quality.
- More complex or larger homes, often featuring multiple stories or high-end finishes, will increase the price accordingly.
- Costs may be higher in areas with stringent building codes or where the cost of living is greater.
Being aware of these variations will help you estimate the potential investment for your specific modular home project. Keep in mind that these figures are just for the home itself and do not account for additional costs that are a necessary part of the building process.
Modular Home Prices
Navigating the realm of modular home prices can initially seem complex due to the various factors influencing costs. Key elements include the size of the home, the design’s complexity, the materials chosen, and the manufacturer’s brand.
Generally, smaller, more basic models offer more affordability, while larger, luxurious designs boost the price tag. It’s also worth noting that regional market conditions and local labor rates play a role in the final cost.
Buyers can expect a base price, but should account for additional expenses such as customization options, which can significantly alter the overall investment. Understanding these components will help buyers make well-informed decisions tailored to their budget and preferences.
Modular Home Cost Per Square Foot
Understanding the cost per square foot for a modular home is essential to budget planning for potential homeowners. Here are the factors that influence this metric:
- Design Complexity: Simple, rectangular designs typically cost less per square foot than complex floor plans with multiple angles or unique architectural features.
- Region: Building costs can vary significantly by location due to local regulations, labor rates, and material costs.
- Finishes and Fixtures: The quality and cost of interior finishes, appliances, and fixtures chosen will impact the overall price.
- Scale of the Home: Larger homes may have a lower cost per square foot due to the cost efficiencies of building at scale.
- Manufacturer and Model: Different manufacturers offer a range of prices, often reflected in the quality of construction and included amenities.
Averaging industry prices, modular homes can range from $70 to over $100 per square foot, underscoring the importance of considering all these factors when determining the expected cost of a modular home.
Custom Design Prefabricated Home Prices
The pricing for custom-designed prefabricated homes varies significantly based on the complexity of the design, the materials chosen, the builder’s rates, and the home’s size.
Here are key points to keep in mind:
- Flexibility in Design: Owners have the freedom to work with architects and designers to tailor floor plans and aesthetics to their preferences, which can influence cost.
- Material Quality and Selection: High-end finishes and sustainable materials can raise the price, whereas standard finishes might be more budget-friendly.
- Size Matters: Larger homes require more materials and labor, directly impacting the final cost. Custom designs frequently feature unique layouts that may not be as cost-efficient as standard ones.
- Builder Selection: Custom prefabs often require a manufacturer with specialized capabilities which may come at a premium. Research and compare various builders to understand their pricing structures.
- Regional Factors: Local regulations, transportation logistics, and site accessibility can also play a role in determining the overall expenses.
- Efficiency Gains: Despite potentially higher upfront costs, savings can be realized long-term through energy efficiency and lower maintenance, which are hallmarks of custom prefab construction.
When budgeting for a custom prefab home, account for these variables to set realistic expectations and ensure your project aligns with your financial plans.
Modular Duplex Cost Estimator
Estimating the cost of a modular duplex involves considering several key factors. The size and complexity of the design directly influence the price, with larger units and more intricate layouts commanding higher costs. Prices fluctuate based on regional labor rates and material prices, so it’s essential to get localized quotes.
Consider these points when evaluating expense:
- Base price per square foot typically ranges between a specified amount, but custom features can push this higher.
- The level of finish, from economical to premium, affects the final cost significantly.
- Site access and land preparation can introduce additional expenses, such as excavation or the need for a more intricate foundation.
- Multiplex modular units, like duplexes, may offer economies of scale, potentially lowering the cost per unit when compared to single-family homes.
- Delivery distance from the manufacturer plays a role, with longer hauls increasing the transport cost.
Understanding these aspects will help in generating a more accurate financial projection for your modular duplex investment.
Story Manufactured Homes Prices
Understanding the pricing for 2-story manufactured homes involves several factors, each influencing the final cost. These homes offer a unique blend of affordability and spacious living, with prices typically ranging from $100,000 to $250,000.
- Design complexity: The more intricate the design, with additional features like multiple bathrooms or a complex roof, the higher the cost.
- Square footage: The price generally scales with the home’s size; expect to pay more per square foot as the size increases.
- Material quality: Higher-end materials will raise the home’s price, whereas more economical materials can keep costs down.
- Brand: Prices can also vary by brand, with some known for luxury finishes demanding a higher price point.
- Regional factors: Labor and material costs, building regulations, and transportation fees will vary depending on location.
- Additional finishes: The level of interior finish, such as flooring, cabinetry, and fixtures, can significantly impact the total cost.
By considering these elements, potential homeowners can get a clearer picture of what a 2-story manufactured home might cost.
Prefab House Kits Prices
Prefab house kits offer an economical and time-efficient solution for potential homeowners seeking to build their new residence. These kits come with most of the components required to construct the home and are categorized by size, design, and features, which all influence the final cost.
A small, basic version typically ranges from $20,000 to $30,000, ideal for those requiring a minimalist space or a secondary dwelling.
Mid-range kits, which offer additional space and customization options, generally cost between $50,000 to $100,000.
Premium kits that boast larger floor plans and luxury finishes can escalate beyond $150,000 depending on complexity and materials.
The price often includes structural elements but may exclude foundations, site work, and finishing touches which need to be accounted for in the overall budget. Modular house kits present an opportunity for hands-on owners to potentially reduce costs by undertaking some of the assembly themselves, provided they have the requisite skills and permissions.
Land & Site Prep Costs
The cost of land is as diverse as its geographical locations, with variables including the proximity to urban centers, land topography, and local real estate market conditions. Acquiring land can constitute a significant portion of your overall budget, often ranging from 25% to 50% of the total project costs.
Site preparation is a crucial step to ensure a strong foundation for your modular home. The complexity of this process will depend on the condition of your land upon purchase. Common tasks include clearing trees, rocks, or existing structures, leveling the ground, and ensuring proper drainage – all of which can impact your budget. Remember, accessing utilities like water, sewer, or septic systems, as well as electrical power, may incur extra costs if they are not readily available.
Environmental assessments might be required to identify potential issues such as soil contamination or endangered species habitats. Permits, which vary by location and are necessary for legal compliance, factor into land and site prep expenses as well.
Typically, the budget for land purchase and preparation ranges from $1.50 to $4 per square foot but can escalate significantly based on the variables mentioned. Factoring in these considerations early in the planning process will help avoid unexpected costs and ensure a smoother project flow.
Modular Home Foundation Cost
When planning for a modular home, it’s essential to consider the foundation’s cost, as this is a critical component of the construction process. Generally, a modular home can be placed on various types of foundations, each with its respective cost implications.
The most common foundation types include:
- Slab Foundation: A slab is a cost-effective option, often cheaper than other foundations due to less labor and material. However, it’s mainly suitable for areas where the ground does not freeze.
- Crawl Space Foundation: A bit more expensive than a slab, a crawl space raises the home off the ground, providing access to wiring and plumbing. It’s beneficial in damp locations or areas prone to termite infestations.
- Full Basement Foundation: This is the most expensive option but adds additional living or storage space to your home. A basement foundation requires significant excavation, formwork, concrete, and reinforcement.
Foundation costs can vary widely based on material prices, labor rates in your region, ground conditions, and the size of the home. For modular construction, other factors like crane rentals for setting the modules may also affect the final cost.
Site preparation is another cost to consider, as it involves levelling the land, digging trenches for the foundation, and possibly installing drainage systems to prevent future water damage.
Always consult with a local contractor for an accurate estimate since they can assess the specific conditions of your building site and provide tailored advice and pricing.
Cost To Deliver A Modular Home
The price to transport a modular home may vary greatly depending on distance, accessibility of the site, and the size of the modules. Generally, short distances result in lower delivery costs, while longer trips, especially those crossing state lines, can increase expenses substantially.
- Distance and Geography: Delivery costs rise with the mileage between the factory and the building site, and if the route includes challenging terrain or congested urban areas, this might further elevate the price.
- Size and Weight: Larger modules require specialized transportation and handling, thus elevating the cost. Moreover, heavier units might demand additional permits or escorts.
- Site Accessibility: Rural or difficult-to-navigate locations can boost the delivery price due to the extra effort or equipment needed to reach the site.
- Permits and Escorts: Some regions demand permits for oversized loads, and in cases where modules exceed certain dimensions, escort vehicles are mandatory, adding to the cost.
Keep in mind that while delivery is a significant cost factor, skimping on a reputable delivery service to cut corners may risk damage to your home, incurring far greater costs in the long run. It’s important to get a detailed quote from your provider that includes all anticipated delivery costs.
Set-Up Cost To Install Prefab Home
Once your modular home arrives, the setup cost is a crucial component of the overall budget. These expenses can vary widely but generally encompass the following:
- Crane Rental: If your module is large or the site conditions are challenging, a crane may be necessary to place the sections onto the foundation. Cost hinges on local rates and the time needed.
- Assembly Fees: Professional crews will connect the modules. This labor can range from simple fastening and sealing to extensive alignment, depending on the complexity of the design.
- Utility Connections: Specialists must hook up your home to electricity, water, sewage, or gas. Prices are contingent on the distance from existing lines and local labor rates.
- Inspection Costs: Post-assembly inspections are mandatory for safety and adherence to local codes, the cost of which may vary by municipality.
Plan for these expenses as part of your modular home installation to avoid unexpected financial surprises once the construction process begins.
HVAC, Electrical & Plumbing Construction Costs
Integrating HVAC, electrical, and plumbing systems into a modular home entails additional costs often not included in the base price. The complexity of design and the quality of materials chosen influence the overall expense.
- HVAC systems vary in efficiency and size, with energy-efficient models commanding higher upfront costs that can lead to long-term savings.
- Electrical installation covers wiring, outlets, and fixtures, with costs scaling based on the home’s size and the customization of lighting designs.
- Plumbing setup involves the in-home network of pipes, water heaters, and often the connection to municipal sewage or a septic system.
- The use of licensed professionals for these installations ensures adherence to building codes and can prevent costly errors.
- Some modular home companies may offer package deals for these services, which can simplify the process and potentially reduce costs.
- Always inquire about the specifics of what’s included in base quotes to accurately budget for the complete installation of these essential systems.
Modular Home Permits
Navigating the permit process is essential to installing your modular home, as it ensures compliance with local building codes and zoning laws. Here’s what to keep in mind:
- Research Local Requirements: Before purchase, check with your local building department to understand specific regulations and fees.
- Cost Variability: Permit costs can vary significantly based on location, home size, and complexity of the design.
- Professional Assistance: Consider hiring a local builder or permit service to manage paperwork and streamline approvals as their familiarity with the process can be invaluable.
- Timeline: Allot adequate time for the permit process as delays can affect your overall project timeline.
- Inspections: Post-installation inspections are usually mandatory, so plan for these to ensure your home meets all necessary standards before you move in.
Basements, Garages, Decks & Other Additions
Expanding the functionality and livability of modular homes can be achieved through various additions, such as basements, garages, and decks. These enhance the home’s value and provide additional space tailored to individual needs.
Basements can offer vital extra square footage for living, storage, or utilities. The cost largely depends on the excavation depth, foundation type, and finishes chosen.
Garages, either attached or detached, provide secure parking and can double as storage or workshop space. The prices vary based on size, materials, and whether it’s pre-built or custom.
Decks create outdoor living areas that can enhance leisure and entertaining opportunities. Material choices, from natural wood to composite, and size are main price factors.
Consider local climate, building codes, and personal preferences when planning these additions to ensure they align with your overall modular home concept and budget.
Adding A Modular Addition To Existing Home Cost
Expanding your living space with a modular addition offers a cost-effective and time-efficient alternative to traditional construction. The price, typically ranging from $100 to $200 per square foot, hinges on customization levels, materials chosen, and overall complexity.
Key considerations affecting cost include:
- Design Complexity: Straightforward designs with standard fixtures and finishes reduce costs.
- Site Accessibility: Easier access to your home site might lower expenses.
- Matching Existing Home: Integrating the addition with the current style can influence the price.
- Foundation Requirements: The need for a new foundation, as opposed to building on an existing one, can increase the overall cost.
- Utilities: Extending and connecting utilities like electric, plumbing, and HVAC systems add to the final price.
In some cases, building a modular addition can lead to savings on labor and materials when compared to stick-built construction, due to the efficiencies of factory production. It’s crucial to consult with a specialist to get an accurate estimate tailored to your project’s specifics.
Modular Vs. Manufactured Homes Cost
When differentiating between modular and manufactured homes, cost variations predominantly stem from the construction process and permanence. Modular homes are typically built to local building codes, similar to site-built homes, and are often permanently installed on a concrete foundation. This parallels traditional home construction and may lead to slightly higher costs due to the materials used and the labor involved. However, modular homes may offer savings through bulk material purchases and efficiency in factory settings.
Conversely, manufactured homes, commonly referred to as mobile homes, adhere to federal HUD code rather than local building regulations. These homes are built on a non-removable steel chassis and can be placed on various foundation types, which can make them less costly initially. The lower price point is due to a more streamlined, less labor-intensive construction process and less stringent building standards.
While manufactured homes can be more affordable upfront, they typically depreciate over time, unlike modular homes, which often appreciate and behave like traditional real estate in terms of valuation. It’s essential to consider these factors when comparing the costs of modular versus manufactured homes to ensure the chosen option aligns with long-term financial and lifestyle goals.
Champion Modular Homes Prices
Champion modular homes are recognized for their affordability and variety. Here’s what to consider:
1. Base Price Factors: Champion’s models start at a certain price point, which primarily depends on the size and design of the home. Expect the base price to cover just the home itself, sans any customizations or upgrades.
2. Customization Costs: While standard designs are more cost-effective, personalizing your modular home will increase the overall expense. Features like premium materials, modern appliances, and smart home technology contribute to a higher price tag.
3. Delivery and Assembly: The distance from the factory to your site influences transportation fees. Additionally, the complexity of assembling different models can affect labor costs, impacting the final price.
4. Region-Specific Pricing: Manufacturing and material costs can vary regionally, so prices in your area may differ from national averages.
5. Series Variations: Champion offers different series of homes that cater to various preferences and budgets, from the more economical Essentials series to the luxurious Titan series, each with their own pricing structure.
6. Time of Year: Seasonal demand can sway pricing, with peak building seasons potentially driving up costs due to higher demand for labor and materials.
By keeping these factors in mind, prospective buyers can better anticipate the affordability and cost implications when considering a Champion modular home.
Stratford Homes Prices and Cost
Stratford Homes has carved a niche in the modular home industry through their commitment to quality and customizable options. Potential homeowners will find that:
- Stratford’s pricing varies depending on factors such as size, design, materials, and finishes. Homebuyers can expect a base price for a standard model and additional costs for any customizations or upgrades.
- On average, prices can range from $200 to $250 per square foot for turnkey construction, which includes both the house itself and additional costs for construction and finishing.
- The company offers a comprehensive list of standard features with each model, and their detailed pricing list helps to clarify what is included in the base price, reducing the chances of unexpected costs.
- For a more precise estimate, it’s recommended to consult directly with Stratford Homes or an authorized dealer, which can also provide information on the costs for preparing the build site, which are not included in the base price of the home.
- Ultimately, the final price will be influenced by local building regulations, site-specific challenges, and each homeowner’s design preferences and choices in terms of fixtures and finishes.
Skyline Homes Prices and Cost
Skyline Homes offers a diverse range of floor plans and customization options, impacting the overall cost of their prefab homes. Prices for these residences generally start at around $50,000 for smaller, single-section models and can exceed $100,000 for larger, multi-section or luxury designs.
Key factors that influence the final price include:
- Size and Layout: Larger homes with more bedrooms or unique layouts typically cost more.
- Custom Features: Upgrades such as high-end finishes, modern appliances, and smart home technology will add to the expense.
- Region: Costs can vary based on local market conditions and the distance from manufacturing facilities.
- Delivery and Installation: Fees are dependent on location and the complexity of the site work needed.
Potential homeowners should consider these variables when budgeting for a Skyline Homes prefab house. It is recommended that they connect with the company or authorized dealers to obtain specific quotations for the models and customizations of interest.
Q: What Makes Pratt Homes Different From Its Competitors?
Pratt Homes sets itself apart in several key aspects:
1. Sustainability Focus: Emphasizing eco-friendly materials and energy-efficient designs to reduce the environmental impact.
2. Customization Options: Offering a wide range of customizable features allowing clients to tailor their homes to their specific tastes and needs.
3. Quality Construction: Commitment to high-quality building standards ensures longevity and durability of the homes.
4. Comprehensive Services: Providing end-to-end solutions from design, construction, to setup ensuring a seamless experience.
5. Local Sourcing: Prioritize the use of locally sourced materials to support community businesses and reduce transportation emissions.
6. Financing Solutions: Partnering with financial institutions to offer affordable financing plans, making home ownership accessible.
7. Family-Owned Touch: As a family-operated business, they ensure a personal approach prioritizing customer satisfaction.
FAQ
How much do most modular homes cost?
The average cost of most modular homes ranges from $180,000 to $360,000, with the majority of homeowners spending approximately $270,000.
What is the average cost of a modular home in Texas?
In Texas, the average cost of a modular home, including installation, ranges from $120,000 to $270,000.
What’s the difference between modular and manufactured homes?
Modular homes are constructed on-site and secured to a foundation, unlike manufactured homes, which are delivered as one whole piece to the site and can be moved, therefore categorized as personal property.
How much are prefab homes in MA?
The average cost of prefab homes in Massachusetts typically ranges from $80 to $130 per square foot, approximately resulting in a total of around $189,000.
What are the cost factors involved in building a modular home?
The cost factors involved in building a modular home include the price of the land, the size and design of the home, the choice of materials, transportation and assembly costs, and any site work like foundations and utilities.
How does the price of a traditional site-built home compare to a modular home?
Modular homes typically cost less than traditional site-built homes due to efficiencies in production and reduced construction time.
What are the long-term savings associated with energy-efficient modular homes?
Energy-efficient modular homes result in long-term savings by reducing energy costs via optimized insulation, efficient appliances, and renewable energy systems that considerably decrease utility bills.
Table of Contents