Last updated on
Discover why modular home prices offer an economical option for prospective homeowners because of their cost-effectiveness, adaptability, and quick construction time.
Key takeaways:
- Modular home prices range from $50,000 to $300,000.
- Cost per square foot ranges from $50 to $100.
- Land and site prep costs include acquisition, permits, clearing, utilities, and access.
- Modular home foundation costs vary based on type and location.
- Delivery and installation costs include transportation, crane rental, professional assembly, and permits.
Average Modular Home Cost
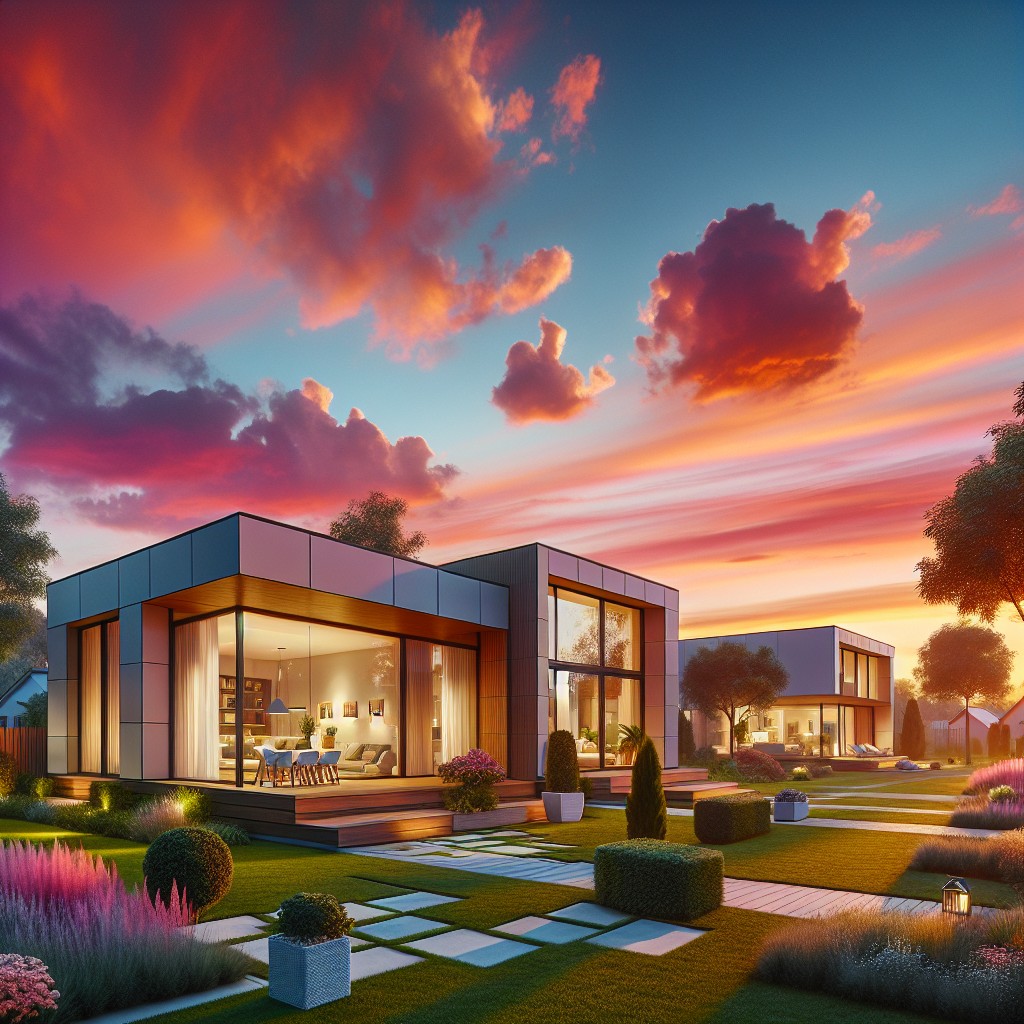
When it comes to the average expense of a modular home, expect a broad spectrum of prices influenced by size, design, and regional factors. Typically, you might see costs ranging from $50,000 for a small, basic model to upwards of $300,000 for a luxurious, custom-designed version. It is essential to note that these figures cover the core modules of the house itself.
- Smaller, more basic designs are at the lower end of the cost scale.
- High-end features, finishes, and custom designs can push prices upward.
- Regional factors, such as labor costs and building codes, can significantly affect the overall price.
- The average cost can serve as a baseline, but a personalized quote will give a more accurate picture for your specific project.
Understanding these points can clarify why there’s no one-size-fits-all price for a modular home and stress the importance of considering personal needs and local conditions in the final cost.
Modular Home Cost Per Square Foot
Understanding the cost per square foot for a modular home can help you budget effectively. Here’s what to consider:
- Base Price: Modular homes typically range between $50 and $100 per square foot for the base price. This usually includes construction, transportation, and builder’s profit, but it’s the starting point before customization.
- Customization: Upgrades and custom features increase costs. High-end finishes, architectural modifications, and larger floor plans can push prices upwards of $150 per square foot.
- Regional Differences: Costs vary by location due to local labor rates, material costs, and building code requirements. Be sure to research costs specific to your area.
By calculating the cost per square foot, you can compare options and understand where your money is going, helping you make informed choices about the size and style of your modular home.
Land & Site Prep Costs
Before your modular home can be installed, the land must be properly prepared. This encompasses a range of vital procedures that vary in cost depending on several factors:
- Acquisition: Purchasing the parcel of land which can vary widely by location.
- Permits: Securing the necessary building permits which have varying costs based on local regulations.
- Clearing and Excavation: Removing trees, rocks, and debris, as well as leveling the site for the foundation, the cost of which hinges on the land’s topography and the amount of work required.
- Utilities: Connecting to existing utilities such as water, sewer, electricity, and gas lines or installing new ones like septic systems or wells if there’s no existing service. This aspect may be more costly in remote areas.
- Access: Building driveways or roads for construction and future access if not already present can add significant expense.
- Impact Studies: In some cases, an environmental impact study may be required before construction can begin.
It’s essential to include these preparatory steps in your budget, recognizing that they can substantially affect the total cost of your modular home project.
Modular Home Foundation Cost
The foundation is a pivotal component for the durability and stability of your modular home, impacting both the cost and the building process’s longevity. Foundations come in various types such as crawl spaces, full basements, or slabs, each having different price implications driven by material requirements and labor.
Crawl Spaces: Often less expensive due to reduced material and excavation needs, they elevate the home slightly off the ground, providing access to utilities.
Slabs: The least expensive option; slabs are quick to construct and require fewer materials than other foundations but offer no under-home storage or utility access.
Full Basements: The most costly choice, they double as additional living or storage space, but entail significant excavation and construction work.
Geographical location, soil type, and local building codes also play roles in cost variation. It’s essential to consult with local contractors to get an accurate estimate tailored to your specific site conditions. Remember, a solid foundation not only supports the home but also contributes to its energy efficiency and moisture control, underscoring the value of investing in a suitable foundation type for your modular home.
Cost To Deliver and Install A Modular Home
Delivery and installation are pivotal cost components that can fluctuate greatly based on distance from the manufacturing location and the complexity of the home.
Transportation Costs: Typically, the charges are calculated per mile. The further the distance, the higher the transportation cost. Also, modular sections are oversized loads requiring special permits and routing which can add to the cost.
Crane Rental: Once on-site, a crane is often necessary to place the modules onto the foundation. The cost depends on the size and complexity of the home, as well as the duration of the crane rental.
Professional Assembly: Skilled contractors will connect the modules, a process which could take several days. This labor will be accounted for in the overall installation costs.
Inspections and Permits: After assembly, local building inspections must be passed before the home is deemed habitable. Ensure that the cost of any necessary permits is factored into your budget.
In summary, these logistical details affect the final price tag and should be considered when planning your modular home budget. Always request detailed quotes up front to avoid unexpected expenses during this phase.
HVAC, Electrical & Plumbing Construction Costs
The integration of HVAC, electrical, and plumbing systems is crucial for your modular home’s functionality. Unlike traditional construction, modules typically come pre-outfitted with these systems, but connection and final setup occur on-site before you can enjoy your new home’s comfort.
HVAC Systems: Heating, ventilation, and air conditioning are essential for climate control. Expect professional installation to ensure efficient thermal regulation and air quality in your home.
Electrical Systems: Every home needs a safe and reliable source of power. Skilled electricians connect module wiring to the main power supply and ensure all outlets, fixtures, and appliances are powered correctly.
Plumbing Systems: To have running water, waste removal, and perhaps gas services, skilled plumbers must carefully connect all modules to the main lines. This also involves setting up fixtures such as sinks, toilets, and showers.
Each of these elements may vary in cost based on the complexity of your modular home’s design and the regional rates for professional services. Selecting energy-efficient systems can save on future utility costs. Always use certified professionals for installation to ensure safety and compliance with local building codes.
Basements, Garages, Decks & Other Additions
Adding a basement, garage, or deck to your modular home can significantly enhance both its functionality and resale value. Here are a few considerations for each:
Basements: A great option for extra living space or storage, adding a basement will increase your upfront costs but can be cost-effective over time. The type of basement—full, daylight, or walkout—affects the price and must be compatible with your land’s topography.
Garages: Whether attached or detached, garages offer secure parking and additional storage. The size and materials used are the main cost variables, but consider future needs like extra workspaces or electric vehicle charging stations.
Decks and Porches: Outdoor living spaces are highly desirable and can be relatively inexpensive extensions to your modular home. Decks made of wood are usually more affordable than those made from composite materials, but consider maintenance and durability when making your choice.
Other Additions: Sunrooms, extra bedrooms, or extended living areas can all be integrated into the initial design. Remember that each addition will involve extra materials, labor, and potential changes to the foundation.
For each of these extras, local building codes, permits, and the home’s design will also influence overall costs. Engage with the modular home manufacturer and local contractors to ensure your desired additions are feasible within your budget and design constraints.
Modular Vs. Manufactured Homes Cost
Understanding the distinction between modular and manufactured homes is crucial for an informed investment. Modular homes are often associated with higher quality standards and are built according to local building codes. This makes their starting price generally higher than manufactured homes, which are built to federal HUD standards.
A manufactured home typically offers a lower entry point in terms of cost. However, its value may depreciate over time unlike modular homes, which can appreciate similarly to traditional stick-built homes.
Consider that modular homes come with the advantage of design flexibility and permanence, often resulting in lower insurance costs compared to their manufactured counterparts.
Lastly, the resell value of modular homes tends to be higher because of their sturdy construction and foundation, mirroring site-built homes. This is an important factor when evaluating the long-term financial implications of your choice.
Factors That Influence Modular Home Cost
Several variables impact the final price tag of a modular home:
1. Design Complexity: Custom designs with intricate layouts or unique architectural details typically come at a higher cost than standard models.
2. Material Quality: Luxury finishes and high-end materials elevate the price, whereas affordable alternatives can lower costs without significantly compromising on aesthetics or functionality.
3. Size and Story: As the square footage increases, so does the price. Additionally, homes with multiple stories require more structural support and staircases, adding to the overall cost.
4. Manufacturer Location: Proximity to the factory can reduce transportation fees. Meanwhile, distant delivery locations may incur higher shipping charges.
5. Regional Costs: Local building codes and labor rates vary; areas with stricter regulations or a higher cost of living can influence the final cost.
6. Energy Efficiency: Investing in energy-saving features (like extra insulation, high-efficiency systems, and renewable energy installations) can bring up the initial cost but lead to long-term savings.
Understanding these factors allows prospective homeowners to better anticipate and manage the budget for their modular home.
How To Cover The Cost Of A Modular Home
Financing a modular home is akin to financing traditional construction, but there are tailored options available. Explore these routes to secure funding:
– Mortgage Loans: Similar to site-built homes, a range of mortgages apply to modular homes, including FHA, VA, and conventional loans. Understand each type’s requirements and choose the best fit for your situation. – Construction Loans: Since modular homes involve building off-site, construction loans can adapt to this by releasing payments in stages. Upon completion, these loans often convert into a traditional mortgage. – Home Manufacturer Financing: Some modular home manufacturers offer financing solutions. Investigate their terms, rates, and benefits, as these packages can streamline the purchasing process. – Personal Savings: If possible, use personal savings to cover down payments or the entire cost to minimize debt and interest paid over time. – Land Equity: In cases where you already own land, consider using it as equity towards your modular home financing.Always compare terms, interest rates, and total loan costs from multiple lenders to ensure you get the best financing possible. It’s prudent to get pre-approved before diving into the home selection process, providing a clear budget and strengthening your buyer position.
FAQ
How much do most modular homes cost?
The average cost of a modular home is $270,000, however, the price can fluctuate based on factors such as square footage, number of stories, number of bedrooms, modular home brand, and costs associated with land preparation, foundation installation, and delivery.
Is it cheaper to build a house or get a modular?
In general, modular homes tend to be less expensive compared to custom-built homes given the same square footage.
How much does a modular home cost pa?
The average cost of a modular home in Pennsylvania ranges from $50 to $90 per square foot.
How much does a modular home cost in Wisconsin?
The average cost of a modular home in Wisconsin is approximately $108,000.
What are the price differences for modular homes across various states in the U.S.?
The price of modular homes varies widely across the U.S., ranging from around $50 to $100 per square foot in southern states like Alabama and Mississippi to upwards of $100 to $160 per square foot in more expensive states like California and New York.
How does the cost of upgrading a modular home compare to a traditional home?
Upgrading a modular home is generally less expensive than a traditional home due to standardized parts and streamlined manufacturing processes.
Are there any hidden costs involved with installing a modular home?
Yes, beyond the base price of a modular home, there can be hidden costs related to land purchase, site work, transportation, construction setup, utilities connection and local permits.
Table of Contents