Last updated on
Exploring kit home prices becomes essential because it allows potential homeowners to make informed financial decisions, reducing the risk of future budget complications.
Understanding the cost of a kit home is crucial – it’s an exciting and cost-effective route for constructing a sustainable, personalized living space. Kit home prices can vary significantly, depending on factors such as size, materials, design, and manufacturer. Estimates often sit between $50 to $300 per square foot, with average-sized homes ranging from $70,000 to $350,000.
Continue and you’ll further uncover the specifics of what influences the price and ultimately, understand how to optimize your budget while still achieving your dream kit home, encompassing every detail necessary for a thorough understanding.
Key takeaways:
- Kit home prices range from $50 to $100 per square foot
- Average-sized kit homes range from $120,000 to $270,000
- Specifications include materials, square footage, and finishes
- Kit homes come in various sizes to suit different needs
- Interior and exterior options allow for personalization
Average Kit Home Cost
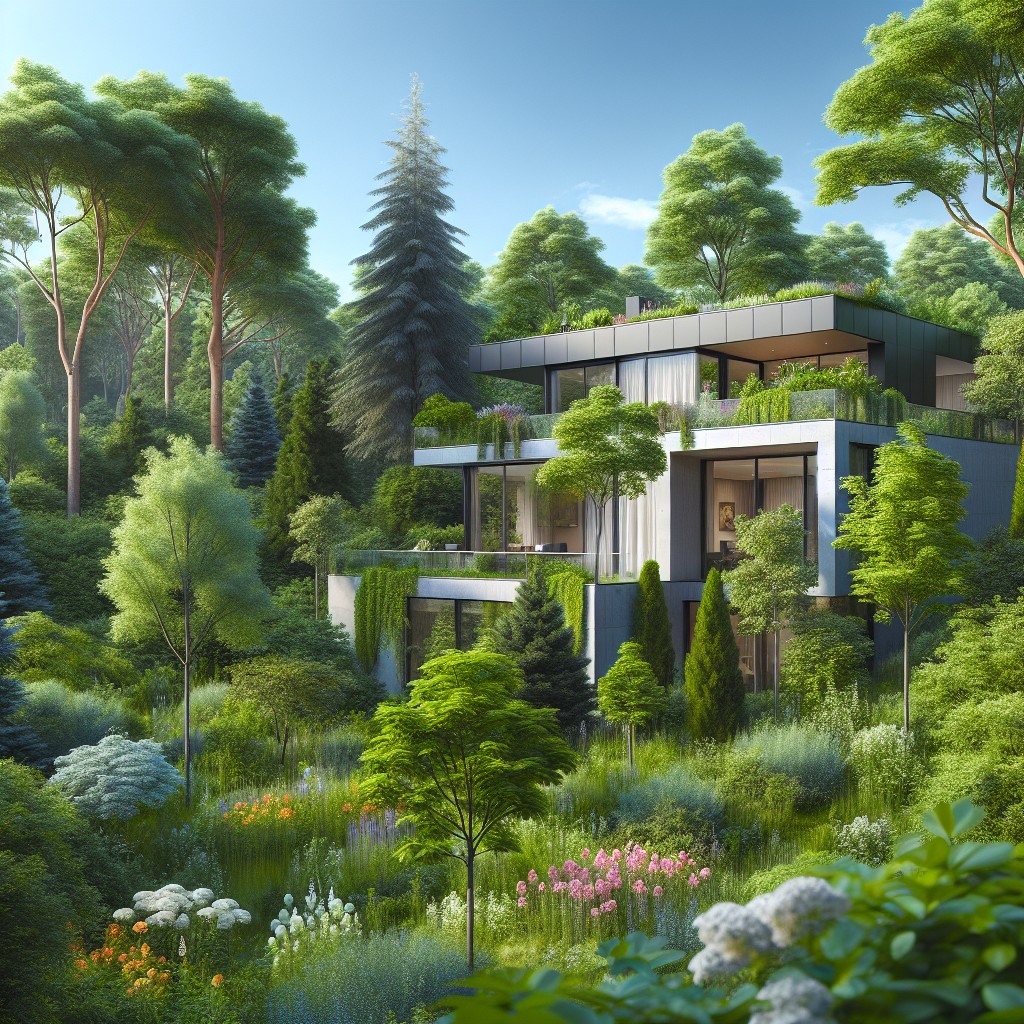
Kit homes present an appealing alternative to traditional home construction, offering potential savings and customization. Prices typically range between $50 to $100 per square foot for just the kit itself. This price point generally includes the shell and basic structure but excludes interior finishes, plumbing, and electrical systems.
When accounting for full installation by contractors, costs may increase to $80 to $160 per square foot, influenced by factors such as design complexity, materials, and labor rates in your area. The price also reflects differences in energy efficiency options and finishes.
On average, expect to invest around $120,000 to $270,000 to complete the entire building process for a kit home. This estimate strikes a balance between affordability and the benefit of customization, making it a cost-effective pathway to homeownership.
Remember that these figures serve as a benchmark; final costs will hinge on personal choices, local regulations, and geographical considerations.
Specifications
When evaluating kit homes, it’s crucial to scrutinize the specifications provided by the manufacturer. These specifications serve as the blueprint for what you can expect in your kit. Essential details include the materials used for construction, such as the type of wood or metal for framing, as well as the insulation rating, which impacts energy efficiency and climate control in your future home.
Square footage is outlined, offering a clear idea of the living space. This factor directly influences the comfort level and possible functionalities of your home. Pay attention to the floor plan designs, which define the layout and room dimensions, affecting the flow and aesthetics of the interior.
Roofing and siding materials are specified, contributing to durability and weather resistance. High-quality materials can significantly increase the lifespan of your home and reduce maintenance costs down the line.
An often-overlooked aspect is the window and door specifications, including their energy ratings and materials, which affect both security and insulation.
Finally, mechanical systems like plumbing and electrical wiring are part of core specs. Some kits include these components pre-installed, while others require additional work by the homeowner or a contractor to complete these systems.
Understanding these details ensures that the kit home you select aligns with your expectations for quality, comfort, and longevity.
Available Sizes
Kit homes come in a myriad of dimensions to suit different space needs and lot sizes. Compact designs start as small as 400 square feet, providing cozy, efficient living spaces perfect for individuals or couples.
Mid-range options often span between 800 to 2,000 square feet, accommodating small families comfortably with multiple bedrooms and living areas.
For those requiring more space, larger models extend up to 3,000 square feet or more, featuring expansive floor plans with several bedrooms, bathrooms, and ample room for amenities.
Customization options allow prospective homeowners to select the ideal size for their lifestyle and property constraints, ensuring that the chosen kit home fits both personal preferences and the physical landscape where it will reside.
Dimensions
When considering the size of your kit home, the choices range considerably. Smaller homes might start at 400 square feet, suitable for a compact living space with minimalistic design. On the other hand, larger structures can exceed 3,000 square feet, ideal for family homes with multiple bedrooms and living areas.
Width and length are key factors; wider and longer homes require larger plots and more materials, potentially increasing costs. It’s vital to balance the desire for space with budget constraints and lot size.
Height is another consideration. Single-story homes are more accessible and can reduce construction complexity. Conversely, multi-story homes maximize vertical space but might necessitate additional structural support.
Keep in mind that while larger dimensions increase living area, they also influence other costs such as foundation requirements, roofing materials, and interior finishing. Choose the size that fits your needs while considering the implications on your overall budget and site requirements.
Interior
Kit homes come with a diverse range of interior options that suit various lifestyles and preferences. You can customize layouts, choose finishes, and decide on fixtures to personalize your space.
- Layouts can be open-plan or sectioned, with the possibility of modifying room sizes and connections according to your needs.
- Finish options typically include different wall treatments, flooring materials, and ceiling designs, offering aesthetic and practical choices.
- Fixtures and fittings, such as cabinetry, lighting, and appliances, are available in eco-friendly and energy-efficient selections, helping homeowners reduce their environmental footprint while maintaining style.
- Energy efficiency is often a key consideration, with options for well-insulated walls, high-quality windows, and doors to reduce heating and cooling costs.
- Home technology integration is also available, with prewiring for smart home systems that allow for convenient control of the home environment.
Selecting the right combination of interior features ensures not only a comfortable living environment but also aligns with sustainability and long-term cost savings.
Exterior
When considering the exterior of a kit home, key factors to take into account include the materials, design, and durability. Materials typically range from wood siding to more modern options like fiber-cement or metal, each with its unique maintenance needs and aesthetic appeal. The design of the exterior should blend with your personal style and the surrounding environment. Options like porches, decks, and color choices can greatly impact the final look.
Additionally, durability is essential to withstand local climate conditions—whether that involves heavy rain, extreme temperatures, or high winds. These facets together contribute to the lifespan and the overall value of your kit home.
Assembly Tools
To successfully construct a kit home, having the right tools is essential. Basic equipment typically includes hammers, screwdrivers, tape measures, levels, and saws for cutting various materials to specifications. Power tools, such as drills and nail guns, can expedite the process, though they require proper safety precautions.
For more extensive builds, specialized tools like pneumatic framing tools, a cement mixer for foundations, or a crane for installing larger sections might be necessary. Renting can be cost-effective for one-time use tools.
It’s important to verify with the manufacturer if any unique tools are required for their assembly process, as these can impact the overall cost and timeline. In some cases, manufacturers might provide tool rental services as part of the kit package, simplifying the process for homeowners.
Always ensure you have a comprehensive toolset ready before beginning construction to avoid delays and ensure a smooth building process. Familiarizing yourself with each tool’s function and handling in advance will also contribute to a more efficient and safer build.
Delivery
When your kit home is ready, the components are packaged and shipped to your building site. Here are some points to consider about the delivery process:
- Check the shipping costs, as they may vary depending on the distance from the manufacturer to your site and the size of your kit.
- Inspect access routes to ensure large trucks can safely reach your property; narrow roads or low-hanging branches could pose issues.
- Coordinate with the delivery company to schedule a drop-off when you or your builder can be onsite to receive and inspect the materials.
- Consider the need for storage in case of delays in construction, as weather and other factors might affect your build timeline.
- Ascertain if the delivery includes unloading assistance or if you’ll need to arrange for equipment or manpower to unload the kit components.
Our Kits & Pricing
Understanding the financial commitment for a kit home is straightforward when you examine the details. The base cost typically ranges from $50 to $100 per square foot. This price generally includes the kit itself, with all the necessary components for the structure. If you opt for a full installation service, the price increases to between $80 and $160 per square foot.
Total expenses can therefore stretch from $120,000 to $270,000 on average, factoring in size and complexity. It’s important to note that these figures are a starting point. Depending on your customizations, finishes, and additional features, the end cost could vary.
When evaluating kits, assess what’s included. Some cover just the bare bones, while others might offer upgraded features or materials. Transparency in pricing is key, so look for companies that detail what exactly the kit entails to ensure it aligns with your expectations and budget.
$50 – $100 Cost Per Square Foot (Unit Only)
Falling within the lower range of the pricing spectrum, the $50 – $100 per square foot cost typically covers the basic kit components without factoring in other substantial expenses. At this price point, you can expect the primary structural elements such as pre-cut lumber, trusses, and sheathing. It’s a more affordable entry into the housing market, suitable for those wanting to take on a hands-on approach with customization and auxiliary choice freedom.
Consider these critical aspects at this price level:
- 1. The shell of the home: You’re mainly paying for the exterior walls, roof, and floor systems. Doors, windows, and interior finishes will be additional costs.
- 2. Customization options: At this stage, plans can often be adjusted, but each modification may impact your total cost.
- 3. DIY potential: This price range caters well to DIY builders, reducing labor costs, but consider your skill level and time availability.
- 4. Exclusions: Be aware that foundations, utilities, and site preparation are not included and will present significant additional expenses.
- 5. Material quality: Materials provided in this tier are often standard quality. High-end, eco-friendly, or specialized materials will increase costs.
Remember, the quoted square footage cost is just the starting point. Be prepared for the additional investments required to transform the kit into a fully functional home.
$80 – $160 Cost Per Square Foot (Full Install)
When opting for a full installation, the price per square foot reflects not just the materials but also the cost of labor and additional services required to transform the kit into a move-in-ready home. Typically, this price range includes:
- Foundation work: Establishing a stable and level base for the home.
- Assembly: Professional construction of the home according to kit specifications.
- Electrical and plumbing: Installation of necessary systems by licensed professionals.
- Interior finishes: Work on floors, walls, and ceilings to create a livable space.
- Exterior finishes: Application of siding, roofing, and paint or other surface treatments.
Choosing this route saves homeowners the time and challenge of managing the construction process themselves and ensures the finished home meets all local building codes and standards. Keep in mind that while this encompasses a comprehensive build, customization or upgrading materials may lead to additional costs.
$120,000 – $270,000 Average Total Cost to Build
Navigating within the average ballpark figures for constructing a kit home, which typically range from $120,000 to $270,000, several critical factors shape the overall cost. The size and design complexity of the chosen kit undeniably play pivotal roles. Larger homes with intricate layouts lead to heightened material and labor costs. The inclusions of high-end finishes and eco-friendly technologies also contribute to an increase in expenses.
Geographical location affects the pricing, considering varying labor rates and material costs by region. Factors such as land topography and accessibility can impact site preparation and foundation work expenses. It’s vital to account for these elements when budgeting, as they can substantially influence the final investment required for your sustainable living space.
The choice between standard and custom kits further sways the total outlay. Standard kits tend to be more cost-effective, but custom options, while pricier, allow for personalization to meet specific needs and preferences. Finally, the extent of professional services used during construction—whether opting for full contractor services or taking on some tasks can also change the cost dynamics significantly. Understanding these parameters helps in making an informed financial plan for your kit home project.
Average Modular Home Cost
When considering the finances for a modular home, ballpark figures are helpful. For every design selected, it’s vital to factor in both square footage pricing and the total project cost.
On average, homeowners can expect to spend between $50 to $100 per square foot for the base unit alone. Yet, once everything is accounted for—including full installation services—this range typically broadens to $80 to $160 per square foot.
Consequently, the overall expenditure for constructing a modular home can range, with most landing between $120,000 and $270,000.
The final price varies widely due to factors such as complexity of design, choice of finishes, and regional differences in labor costs. Keep in mind that these prices do not account for land acquisition, site preparation, or potential upgrades and customizations.
It’s crucial to consider these variables alongside the base costs to ensure an accurate budget for your modular home project.
Modular Home Plans and Prices List
When exploring modular home plans, you’ll find a broad spectrum, from compact designs to expansive multi-story floor plans. Prices typically hinge on the complexity of the design and the square footage.
A basic single-story might start from about $50,000, offering a few hundred square feet—ideal for those prioritizing economy and simplicity.
For larger designs, such as family homes with multiple bedrooms, expect prices to shift upwards to $100,000 or more, not accounting for customization options that can further inflate the cost. The allure of two-story models can escalate costs significantly due to additional structural support and complex assembly requirements, often pushing the price tag above $150,000.
A considerable advantage of modular homes is the catalog of pre-designed options, which not only streamline the decision process but can contain costs by avoiding the premiums of bespoke designs. Nonetheless, most providers will customize plans to varying degrees, striking a balance between personalization and cost-effectiveness.
Keep in mind that these prices generally cover the core structure only. Essential add-ons such as foundations, utility connections, and site preparation will affect the final cost. It’s vital to factor these into your budget early in the planning process to get a realistic picture of the total investment.
Custom Design Prefabricated Home Prices
Embarking on the journey of a custom-designed prefabricated home allows for personalization reflecting individual style and needs. The price for this level of customization starts in the range of $100 to $200 per square foot and can climb higher based on design complexity, materials, and finishes chosen.
Key factors influencing cost include:
- Architectural design fees: Collaborating with architects results in a fee for creating a unique home.
- Material selections: Opting for high-end finishes like hardwood floors or granite countertops can elevate costs.
- Size and complexity: Larger homes with intricate designs lead to higher manufacturing and assembly costs.
- Energy-efficient features: Investments in sustainability, through solar panels or geothermal systems, for instance, can be costlier upfront but provide long-term savings.
- Site-related expenses: Preparing land for a custom prefab involves variable costs based on topography, accessibility, and the need for utility connections.
Understanding these components will help set realistic budgets for creating a personalized, structured living space tailored to your requirements and aesthetic choices.
Small Modular Home Prices
Starting with the more compact options, small modular homes offer a blend of affordability and efficiency, making them a sought-after choice for individuals, couples, or small families. Typically ranging from 600 to 1,200 square feet, these homes can deliver the essentials without excessive space that could drive up costs.
- Cost Factors: The price is influenced by design complexity, materials used, and additional features like eco-friendly options or smart home technology.
- Price Range: Small modular homes are usually priced between $50,000 and $150,000 for the base model units, excluding land, foundation, and installation.
- Transportation and Installation: While they benefit from economies of scale in manufacturing, remember to account for delivery expenses and the cost of crane rental for setting the modules in place.
- Customization: Standard layouts keep prices down, but customization can increase the cost; it’s a trade-off between personal taste and budget constraints.
- Speed of Construction: Quicker build times often translate to labor cost savings, making these homes a wise investment for those on a stringent timeline.
- Long-Term Savings: Investing in energy-efficient options may raise the initial price but can result in significant utility savings over time.
Exploring small modular home options often reveals a wide market range—from basic models to those that exude luxury in a smaller footprint. Understanding what drives the cost will help in making an informed decision that aligns with both needs and budget.
Story Manufactured Homes Prices
Two-story manufactured homes offer expanded living space and design versatility, often fitting within smaller land plots because they build vertically. Generally, these homes have a higher price point compared to their single-story counterparts due to the additional square footage and complexity of structure. Prices typically range from $100 to $200 per square foot, depending on the level of customization and regional market factors.
To break down the costs further:
- Base price includes the core structure, roofing, and primary interior finishes.
- Customization, such as upgraded finishes or additional architectural features, will impact the final price.
- Additional costs can include onsite assembly and connection to utilities, which vary by location and complexity of the site.
It’s also essential to remember that the quoted price often excludes land purchase, foundation work, and other site preparations needed before installation. These expenses must be calculated separately to understand the complete investment.
Land & Site Prep Costs
Securing a plot for your kit home is just the beginning. Before construction can commence, the site needs proper preparation, which entails a range of activities pivotal for the successful installation of the home. The complexity and cost of these activities can significantly affect your overall budget.
1. Evaluation and Clearing: It’s essential to evaluate the land for suitability. Costs may include professional assessments, clearing trees, and removing rocks or debris to establish a buildable area.
2. Access and Infrastructure: If your site lacks access to public roads, additional costs may arise from creating a driveway. Moreover, you’ll need to establish connections to utilities such as water, sewage, power, and possibly gas.
3. Groundwork and Leveling: Preparing a stable foundation requires proper grading and leveling. This step might also include excavation for a basement if your design calls for it.
4. Foundation Construction: The type of foundation you choose—slab, crawl space, or basement—will impact costs. Concrete foundations typically incur material and labor fees.
5. Impact Fees: Be aware these fees are charged by local governments to cover the increased public services required by your new home.
6. Consents and Permits: Local regulations may necessitate certain permits for construction, water use, and sewage treatment, adding to the prep costs.
Understanding these variables allows you to plan financially for the site work phase—an integral part of your kit home project.
Modular Home Foundation Cost
The foundation is critical in ensuring the longevity and stability of a modular home. Costs vary based on the type of foundation you select:
1. Slab Foundation: Typically the least expensive option, a concrete slab may cost between $4,500 and $12,000, factoring in size and thickness.
2. Crawl Space Foundation: Ranging from $8,000 to $21,000, a crawl space elevates the home off the ground, providing access to plumbing and electrical systems.
3. Basement Foundation: The most costly option, starting from $18,000 up to $30,000 or more, a full basement adds significant square footage, but its expense reflects the additional labor and materials required.
Site work can affect the final cost, with factors including excavation, grading, and the need for retaining walls. Soil testing is also vital before construction begins; inadequate soil conditions might demand a more robust foundation, impacting the total expense. Local building codes and environmental regulations can further influence foundation costs. Always incorporate a contingency fund for unforeseen expenses, generally an additional 10-15% of the foundation cost.
Cost To Deliver A Modular Home
When considering the delivery of a modular home, distance is a key cost factor. Transporting the home’s sections from the factory to your building site typically incurs a charge-per-mile fee. The geographical terrain and accessibility of your site may also influence the final cost, potentially requiring specialized vehicles or additional labor to navigate challenging roads or obstacles.
Additionally, the number of modules to be transported plays a part in the expense; more units lead to higher delivery costs. It’s important to coordinate with your manufacturer to understand their delivery radius and any potential surcharges for long-distance transportation.
Finally, state regulations can impact delivery costs. Certain states require escort vehicles for oversized loads, adding to the total expense. Be sure to account for these factors when budgeting for your modular home project.
FAQ
How much did kit houses cost?
In the 1920s, kit houses sold by Sears, Roebuck ranged in cost from approximately $600 to $6,000, translating to around $8,400 to $84,000 in current currency.
Is it cheaper to build with a kit?
Yes, building with a kit can be more cost-effective than constructing traditional houses due to their similar business models to modular and manufactured homes.
How much do most modular homes cost?
The average cost of constructing a modular home is typically between $180,000 and $360,000, with an average expense of $270,000, depending on the square footage, land cost, and any additional fees.
Is it cheaper to build or buy prefab?
Building with prefab homes is generally cheaper than traditional construction, with prefab options being about 10% – 20% less expensive and reducing on-site construction time.
What factors influence the price of a sustainable kit home?
The price of a sustainable kit home is influenced by factors such as the size, design, materials used, location for construction, and requested customizations.
How does site preparation affect the overall cost of erecting a kit house?
Site preparation significantly affects the overall cost of erecting a kit house as it involves processes like land clearing, excavation, and soil testing that can increase expenditures.
How do customization options impact the final price of modular homes?
Customization options significantly impact the final price of modular homes as modifications to standard designs often require additional resources and labor, leading to higher costs.
Related reading:
Table of Contents