Last updated on
Severe weather, floods, fires, mold, or other threats can damage structures of any size. However, the damage recovery process looks different for large industrial facilities than smaller residential or commercial properties.
Industrial sites—like factories or power plants—require specialized cleanup, repair, and restoration techniques. Fortunately, the six action steps below will minimize the downtime and guarantee a safe return to full operations.
Initial Damage Assessment and Cleanup
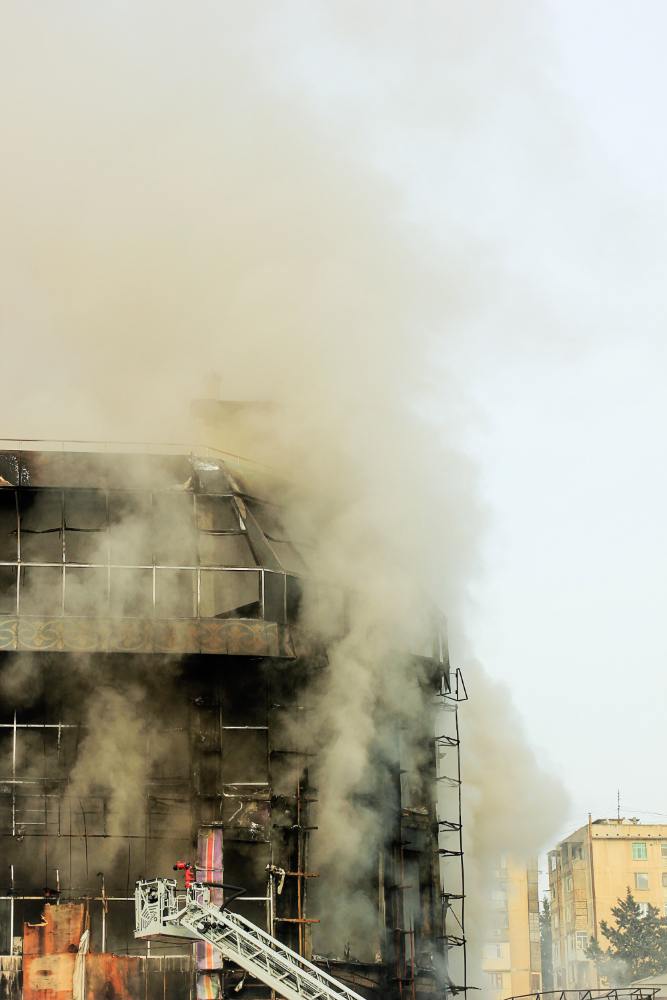
The first step in industrial construction recovery is enlisting qualified professionals to assess damage. This evaluation will help determine the extent of damage so your team can outline a comprehensive recovery plan.
After that initial assessment, cleanup crews can secure the premises, remove debris, extract standing water, and perform other cleaning tasks. Securing the site will prevent further structural damage so the remaining recovery work can proceed safely and efficiently.
Structural Stabilization and Repairs
Before starting the remediation, repair damage to the industrial facility’s core structure. Depending on the damage’s nature and severity, this process could involve boarding up windows, tarping roofs, shoring up walls, or repairing the framework.
Minor fixes will suffice sometimes, but major reconstruction might be necessary in others. Consult an expert restoration service to ensure structural integrity and safety.
Restoration of Interior Materials and Contents
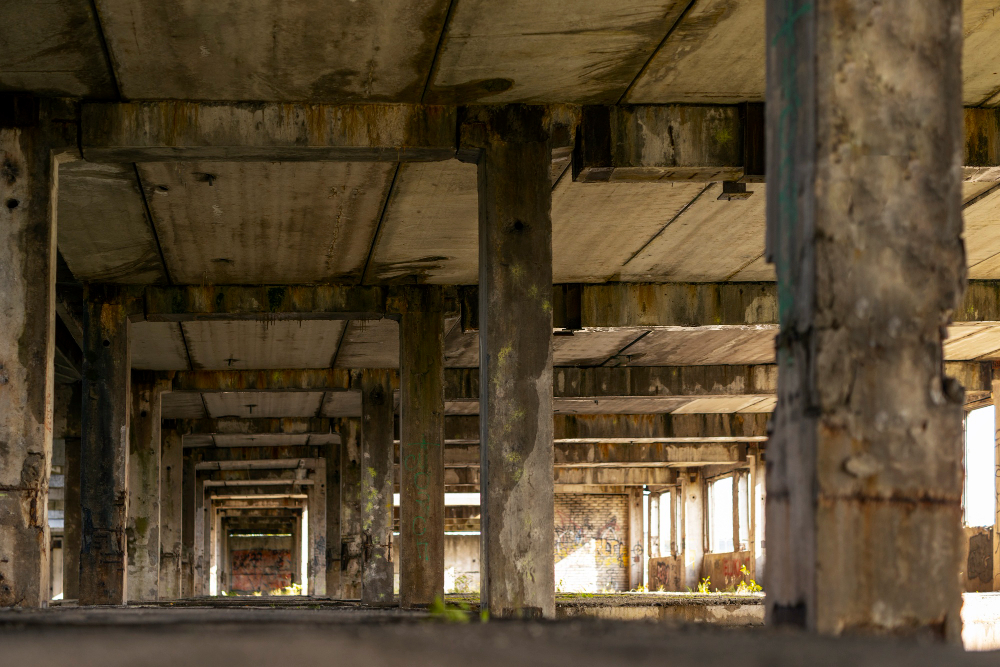
Once the structural repairs are complete, focus on restoring the industrial facility’s interior contents and materials. Treat water damage with professional-grade drying equipment to minimize the risk of further deterioration or potential mold growth.
Meticulously clean all surfaces affected by smoke and soot to remove residue or odors. If mold is present, call in a professional remediation service to eliminate the growth and prevent recurrence. Then, clean and repair salvageable machinery or equipment to its working condition. The ultimate goal of this phase is to restore the facility to its pre-damage state.
Replacement of Unsalvageable Materials
Despite the most vigorous efforts of restoration professionals, some materials might not be repairable and will, therefore, need replacement. In the case of severe issues, you might have to install new flooring, drywall, ceiling tiles, furniture, or specialized equipment.
Carefully dispose of these unsalvageable items to prevent contamination and ensure a clean, safe environment. Then, install the new materials with care, precision, and attention to detail to seamlessly integrate with the restored portions of this facility.
Final Cleaning and Decontamination
Before the industrial facility is reoccupied, the entire space must undergo a final cleaning, sanitization, and decontamination process. This process includes cleaning all surfaces, remediating residual odors, and performing infection control procedures to ensure a healthy environment for all occupants.
Also, consider third-party testing for contaminants like mold, bacteria, lead, or asbestos to confirm the efficacy of all cleaning and remediation efforts.
Inspections and Re-occupancy
The last step before resuming operations is to obtain re-occupancy clearance through various inspections, such as code evaluations, air quality tests, health and safety audits, equipment checks, and more.
The inspections or tests required might vary based on the nature of the facility and the extent of damage. As soon as you pass all these inspection clearances, the industrial facility can reopen for business.
Follow These Steps for Successful Industrial Damage Recovery
Recovering from industrial construction damage requires specialized expertise, meticulous planning, and a reliable commitment to health and safety. While the process can be daunting, businesses that tackle these distinct recovery phases thoroughly and proactively stand a better chance of successfully resuming operations.
By maintaining occupant safety, collaborating with restoration professionals, and complying with other best practices, industrial facilities can minimize disruption, restore efficient workflows, and emerge from this process as a stronger, more resilient enterprise.
Table of Contents