Last updated on
Understanding the costs associated with constructing a 500 sq ft accessory dwelling unit (ADU) is crucial for homeowners looking to expand their living space efficiently and economically.
Key takeaways:
- ADU size impacts cost: Layout, economy of scale, regulations, materials.
- Construction type affects cost: Stick-built vs. prefab, materials, foundation.
- Prefab ADUs offer cost and time savings.
- Cost comparison: Prefab vs. site-built ADUs.
- Cost estimation methods: Cost-per-square-foot, modular pricing, itemized quotes.
ADU Size
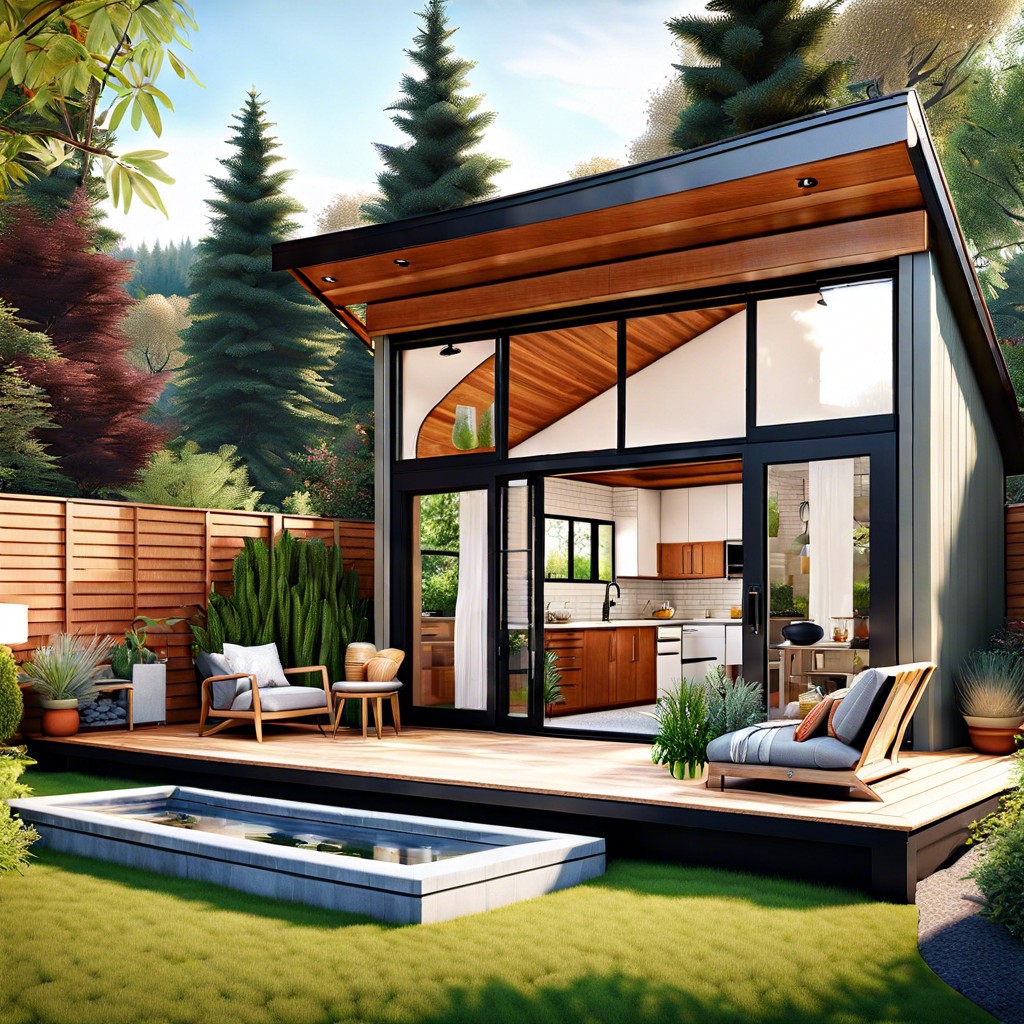
Understanding the impact of ADU size on the overall cost is critical. While 500 square feet may seem modest, every square foot adds to the materials and labor required. Here’s what to consider:
- Layout Efficiency: Smaller spaces need smarter designs to maximize functionality. Engage with a design that utilizes every inch effectively, as custom layouts can drive up costs.
- Economy of Scale: Larger ADUs can sometimes have a lower cost per square foot due to the economy of scale. However, a 500 sq ft unit strikes a balance, offering enough space for essential amenities while keeping the budget manageable.
- Regulatory Constraints: Check local zoning laws, as they may influence the cost. Some areas have impact fees that are independent of ADU size, making larger ADUs relatively less expensive in terms of fees per square foot.
- Systems and Fixtures: Even in small ADUs, you’ll need a fully functioning kitchen, bathroom, and HVAC system, which are significant cost components regardless of size.
- Material Choices: The cost of finishes will affect your budget. Opt for materials that are both durable and cost-effective without compromising on aesthetics or quality.
Bear in mind, the number of rooms or the inclusion of luxury amenities can substantially alter the cost, regardless of the ADU’s overall footprint. Insightful planning will ensure your 500 sq ft ADU is both financially and spatially optimized.
Construction Type
The choice of construction type has a significant impact on the overall cost of a 500 sq ft ADU. Two primary approaches include traditional stick-built homes and modular construction. Stick-built ADUs involve on-site construction with materials delivered to the location, which provides customization freedom but often comes with higher labor and material costs. On the other hand, modular or prefab ADUs are manufactured off-site and assembled on the property, often leading to reduced construction time and potential cost savings.
Material selection also affects the budget. Using high-end finishes or opting for eco-friendly materials can drive up costs, while more standard, locally sourced materials may help keep expenses down. Additionally, foundation type—whether a slab, crawl space, or basement—is another cost variable. A slab foundation is typically the most cost-effective, whereas basements can significantly increase the overall price tag due to deeper excavation and more complex construction.
It’s important to factor in the complexity of design as well. A straightforward, rectangular layout with minimal architectural details will be less expensive than a complex design with multiple stories, unique shapes, or custom features. Lastly, consider the integration of systems such as plumbing, electrical, and HVAC. An ADU that shares utilities with the main house might save on upfront costs, whereas completely independent systems will add to the overall budget but may offer greater long-term flexibility and tenant privacy.
What Is a Prefab ADU?
A prefab ADU, or prefabricated accessory dwelling unit, is a secondary housing structure constructed with factory-made components that are assembled on-site, similar to building with Lego blocks. This construction method offers streamlined production processes, increased efficiency, and often results in a quicker turnaround from start to finish compared to traditional stick-built homes.
The components for prefab ADUs are built in a controlled environment, which reduces the potential for on-site construction delays due to weather or scheduling conflicts. Factory settings also allow for stricter quality control, ensuring that each part of the ADU meets specific standards before it leaves the warehouse.
Transported to the property in large sections or as a nearly complete unit, prefab ADUs require significantly less on-site construction time, translating to less labor cost and quicker occupancy. Additionally, the prefab process is known for generating less waste, making it a more environmentally friendly option for expanding living space.
Which Is Cheaper: A Prefab or Site Built ADU?
When comparing the costs of prefabricated (prefab) ADUs versus site-built ADUs, several factors come into play. Prefab ADUs are typically more cost-effective due to standardized building processes and bulk material purchasing, which reduces waste and overage costs. The streamlined manufacturing of prefab units also lessens the likelihood of weather-related construction delays, thus saving time and potentially associated labor costs.
On the other hand, site-built ADUs provide the opportunity for customization that can match the existing property aesthetics more seamlessly. This benefit, however, often comes at a higher price point. The on-site construction involves variable labor rates, material delivery costs, and sometimes unpredictable challenges that can arise during the building process, all of which can contribute to a higher overall cost.
Importantly, economies of scale can affect the cost comparison. For individuals building a single ADU, the prefab route may offer significant savings. But for developers or individuals who are constructing multiple site-built ADUs concurrently, the cost difference might narrow due to the efficiency of having tradespeople and equipment already mobilized on the site.
In regions where labor is in short supply or very expensive, prefab units might be the only viable option. Conversely, in areas with lower labor rates and plenty of available contractors, site-built ADUs could be comparable or even cheaper than prefab options, especially when considering potential shipping fees for prefab units.
Ultimately, the cheapest option can depend largely on the specifics of your location, your access to contractors and materials, and your personal preferences for customization and building speed. It’s essential to get detailed quotes for both options and consider the total cost implications before making a decision.
Ways to Cost Accessory Dwelling Units (ADUs)
Calculating the cost of an ADU involves multiple approaches depending on the nature of the project and personal preferences. Knowing these methods can help streamline your budgeting process.
One common way is the cost-per-square-foot method, which multiplies the total area (square footage) of the ADU by the average cost per square foot for building in your area. This gives a rough estimate that should be adjusted according to the quality and type of finishes you intend to use.
Modular ADUs offer a different pricing approach. They usually come with a fixed price that includes the cost of manufacturing and sometimes the cost of on-site assembly. Add-ons, upgraded finishes, and foundational work are extras that you should account for separately.
Lastly, itemized quotes from contractors provide the most detailed cost assessment. It lists all the expenses associated with the ADU construction including materials, labor, permits, and additional fees. While this method can be time-consuming, it offers the clearest picture of where every dollar is going.
Each method has pros and cons, but a balanced combination of the three can yield the most accurate cost estimation for your ADU project. Keep in mind that flexibility is key as unforeseen costs are common in construction.
Table of Contents