Last updated on
Explore the potential of 3D-printed houses in this article, delving into the world of sustainable architecture because these innovative structures offer substantial benefits in terms of efficiency, waste reduction, and design flexibility.
I have created these unique designs for your inspiration. I hope you will enjoy them!
Diving headfirst into the uncharted waters of 3D printed houses, this piece intends to not just follow but blur and even redraw the standard guidelines. While an appreciation of existing blueprints remains, the ultimate objective here is to stir the pot, adding splashes of fresh, unique ideas.
Navigating through the multitude of online suggestions, we’ll carve our path, shining a spotlight on new angles and perspectives. Whether you’re acquainted with the concept or just dipping your toes into this realm, the objective remains the same – to enlighten, inspire and hopefully, surprise you.
An amalgamation of the best-established ideas sourced from comprehensive internet research will be provided at the end of this write-up as promised. Without further ado, let’s unveil a fresh list of 3D print house propositions, churned right from the innovation factory.
The Role of 3D Printing in the Future of Sustainable Architecture
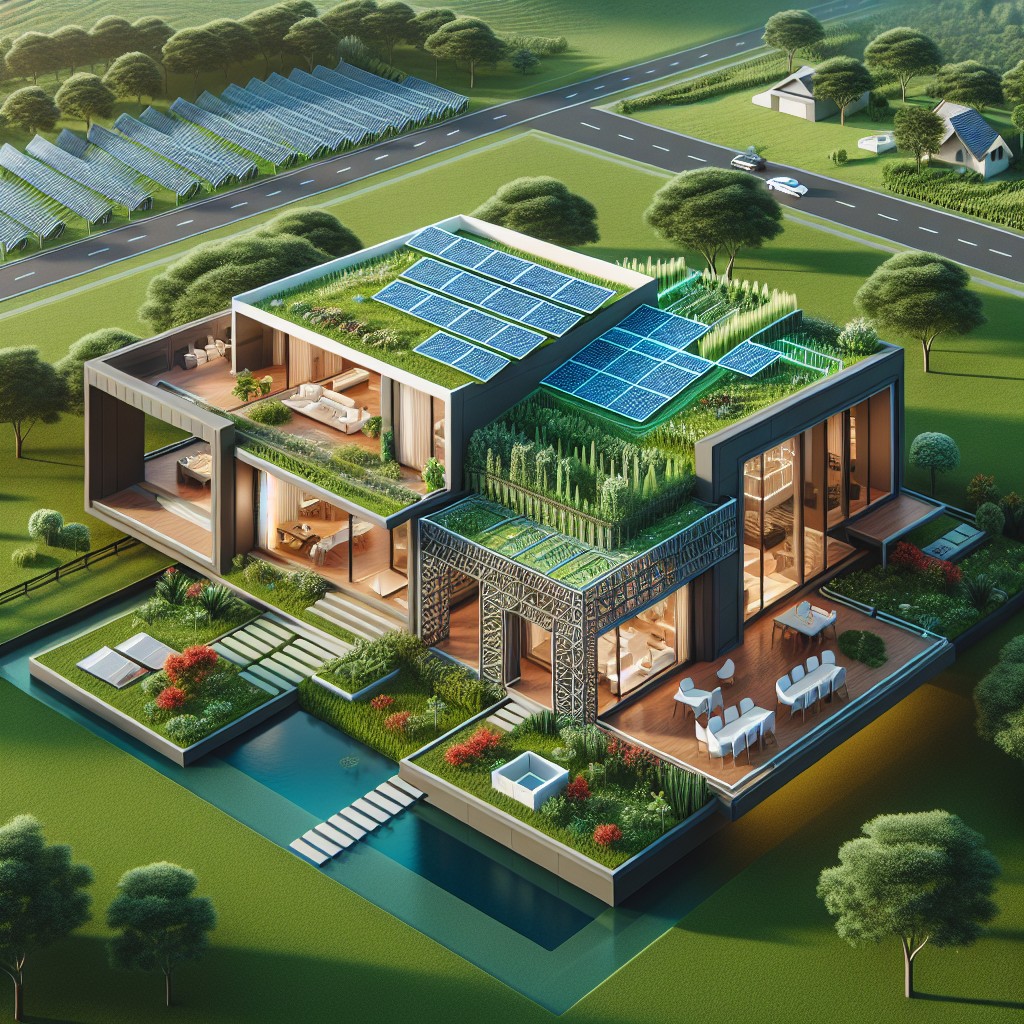
3D printing technology promises a revolution in sustainable architecture by offering bespoke design options while reducing material waste. This innovative construction approach significantly minimizes the carbon footprint associated with traditional building methods.
Here’s why:
- Tailored Insulation: Customized wall structures with built-in insulation can be printed, optimizing energy efficiency.
- Reduced Transportation Emissions: Local production of materials cuts down on long-distance transport.
- Minimal Material Waste: Precise printing means resources are used only as needed, unlike conventional construction which often results in surplus.
- Durability and Upcycling: 3D-printed structures can be designed for longevity and eventually, materials can be recycled for new constructions.
- Biodiversity Preservation: With precise placement of materials, natural habitats can be less disrupted during the building process.
Harnessing 3D printing for sustainable architecture not only brings cleaner construction practices but also sparks innovation in designing homes that live in harmony with the environment.
Comparison of Different Materials for 3D-Printed Houses
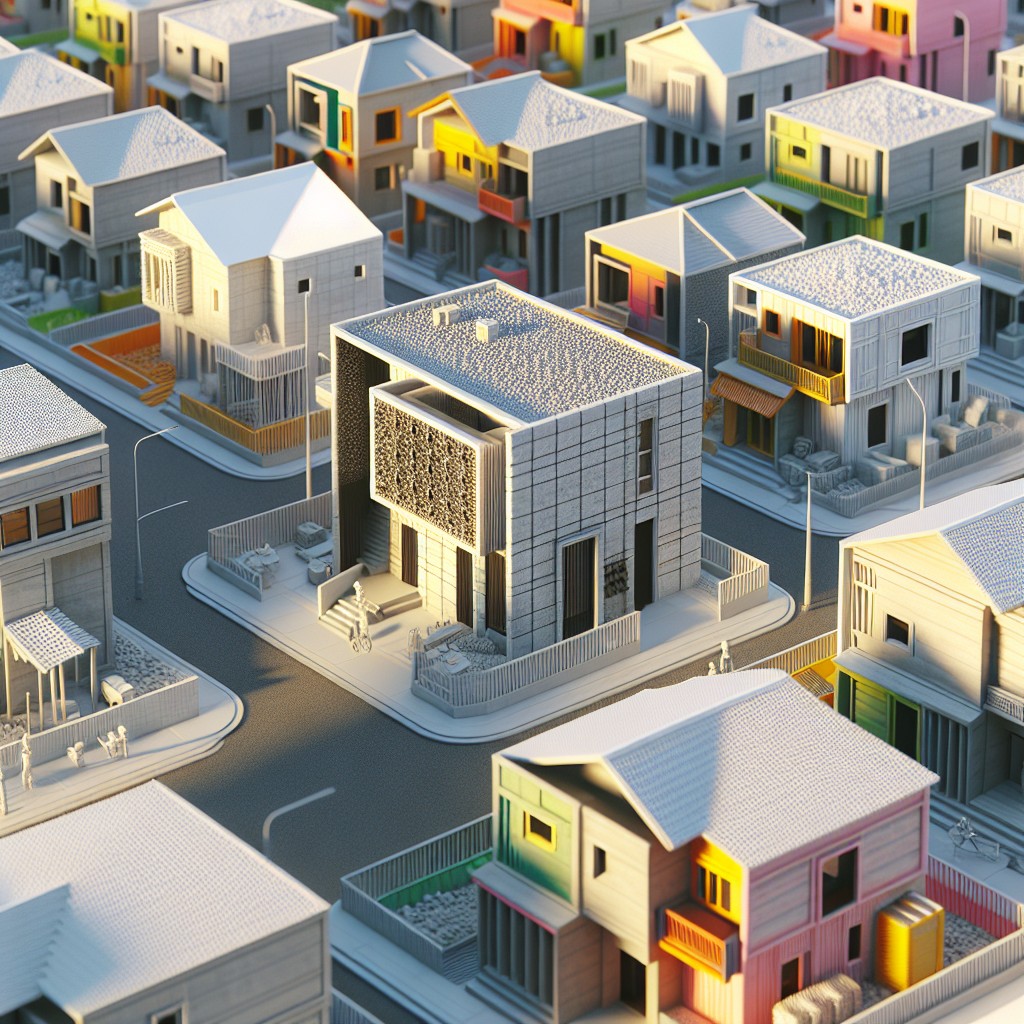
In the realm of 3D-printed construction, material choice is a key determinant of sustainability, durability, and cost. Typically, construction-grade plastics, concrete, and earth-based materials are the frontrunners.
Construction-Grade Plastics: These include recycled polymers which are lauded for their lightweight properties and resistance to moisture, making them suitable for wet climates. However, they may not offer the structural integrity required for larger buildings.
Concrete: A favorite for its robustness and fire resistance, concrete can be optimized for 3D printing, ensuring a quicker build. It’s ideal for creating solid walls with good thermal mass, but its weight necessitates a strong foundation.
Earth-Based Materials: Innovations involve the use of local soil mixed with sustainable binders—lowering transportation emissions and tapping into traditional adobe construction methods. This technique champions environmental consciousness and can be optimized for thermal performance.
Choosing the right material shapes the building’s environmental footprint, structural capability, and energy efficiency. The decision hinges on the specific requirements of the project and the locale’s resources and regulations.
The Impact of 3D-Printed Houses On the Real Estate Market
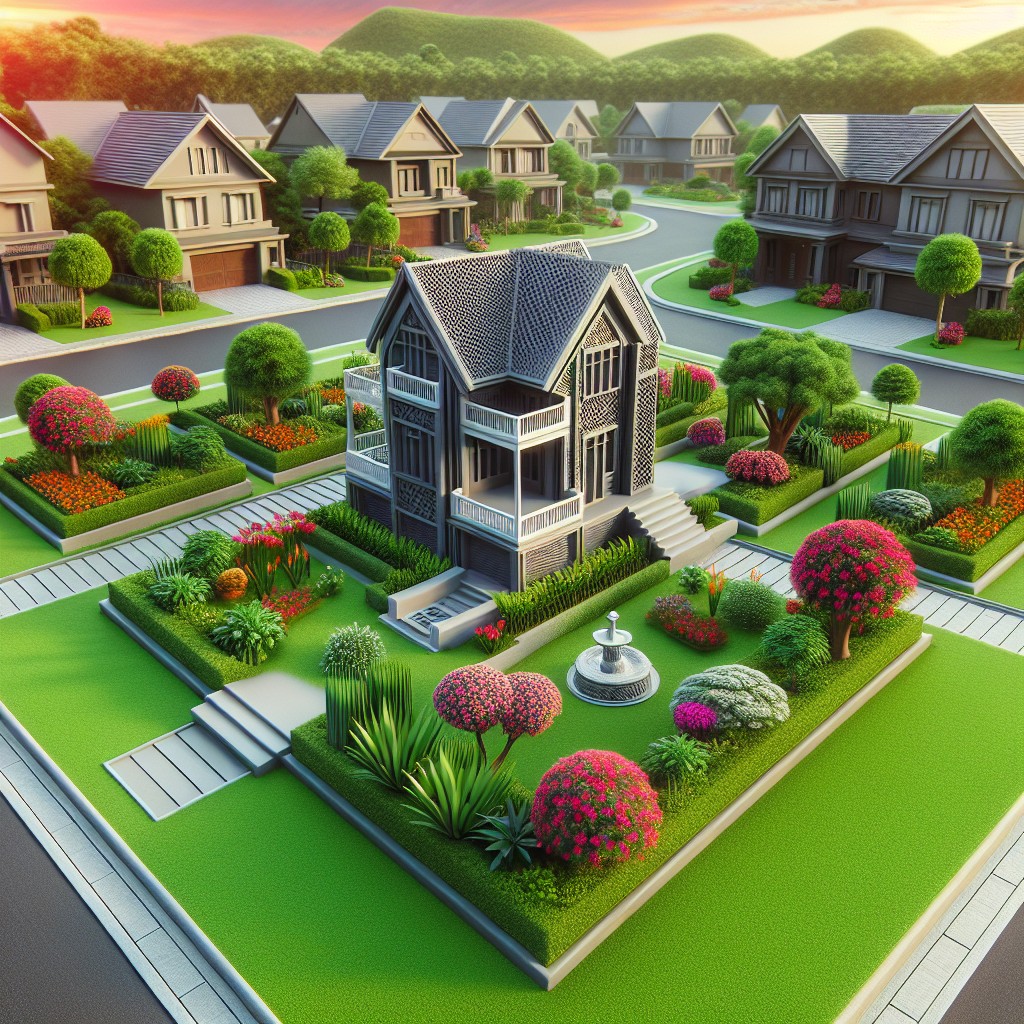
The advent of 3D-printed houses ushers in a paradigm shift in the real estate market. As construction speeds increase, homes may soon be built in a matter of days rather than months, potentially reducing overall market supply shortages. This technology delivers cost-efficiency, passing savings on materials and labor to the consumer, likely making homeownership more accessible to a broader demographic.
Moreover, 3D printing introduces an unprecedented level of design customization. This flexibility allows buyers to personalize their future homes, which can adjust market demands towards more individualized properties. As investors and developers harness this technology, we may witness a diversification of housing stock, shaking up traditional real estate models.
However, the technology also brings fresh challenges. Appraisals and financing methods will need to evolve to accommodate houses that do not fit conventional construction norms. Further, existing infrastructure may require updates to support the development of 3D-printed communities. Real estate professionals must stay abreast of these changes to navigate the evolving landscape effectively.
How 3D Printing Revolutionizes Affordable Housing
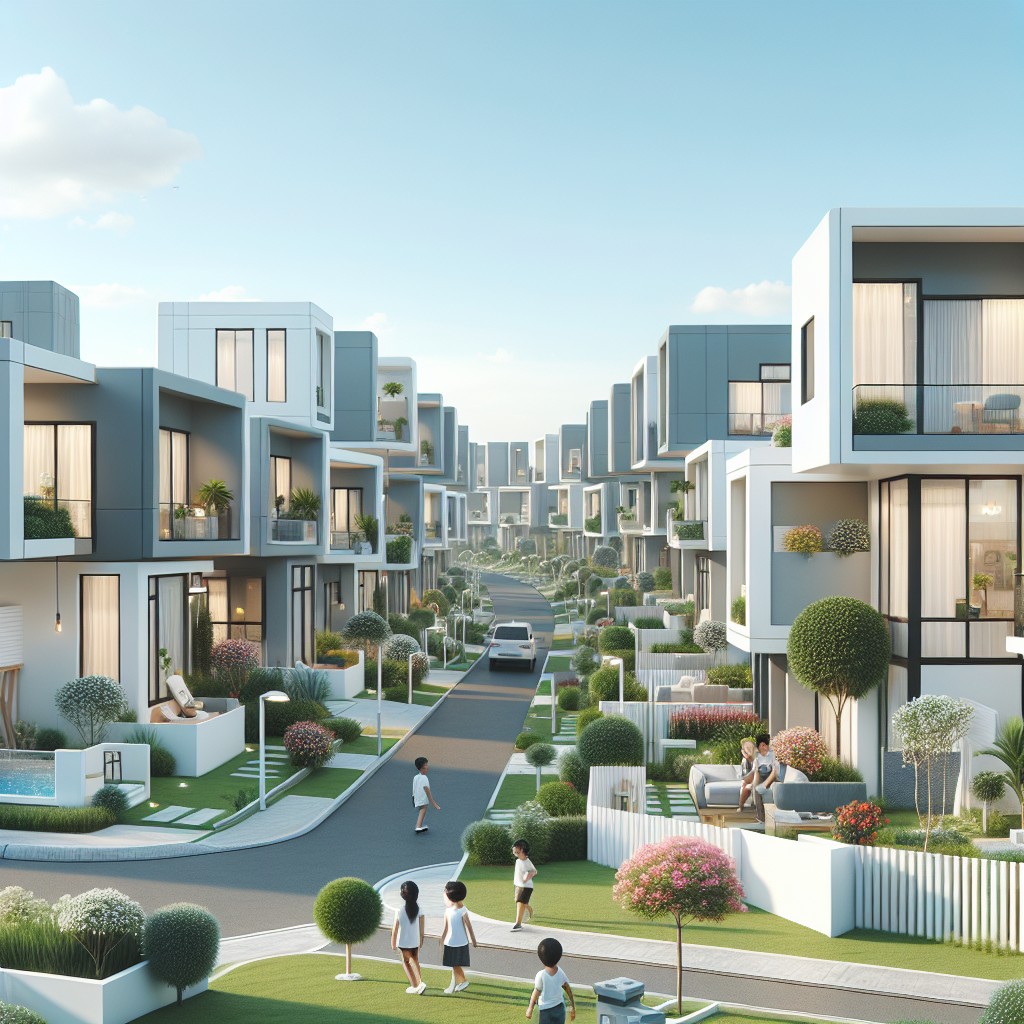
The advent of 3D printing technology in construction heralds significant cost savings, opening doors to affordable housing solutions worldwide. Here’s a concise exploration of the factors that contribute to these cost reductions:
- Reduced Material Waste: Traditional construction often leaves a surplus of materials, which means paying for more than what is actually incorporated into the structure. 3D printing precisely deposits materials, minimizing waste and associated costs.
- Labor Efficiency: Automating the building process reduces the need for a large construction crew. A 3D printer can be operated by a smaller team, decreasing labor expenses remarkably.
- Speed of Construction: A 3D printer works around the clock, completing structures in a fraction of the time taken by conventional methods. This speed translates to lower costs in terms of both labor and the rental of construction equipment.
- Design Flexibility: 3D printing software enables the creation of complex designs without a corresponding increase in cost, making it easier to design homes that utilize resources like natural light and heat more efficiently.
- Material Costs: The technology can utilize a range of materials, some of which may be sourced locally or consist of sustainable resources like recycled plastics, further cutting down expenses.
- On-site Printing: Transporting large materials or pre-made elements to a building site can be costly. With 3D printing, homes can be constructed on-site, eliminating these transportation costs.
These elements coalesce to make the 3D printing of homes a game-changer for affordable housing, offering a beacon of hope to tackle housing shortages without breaking the bank.
3D-printed Accessories and Furnishing to Complement 3D-printed Houses
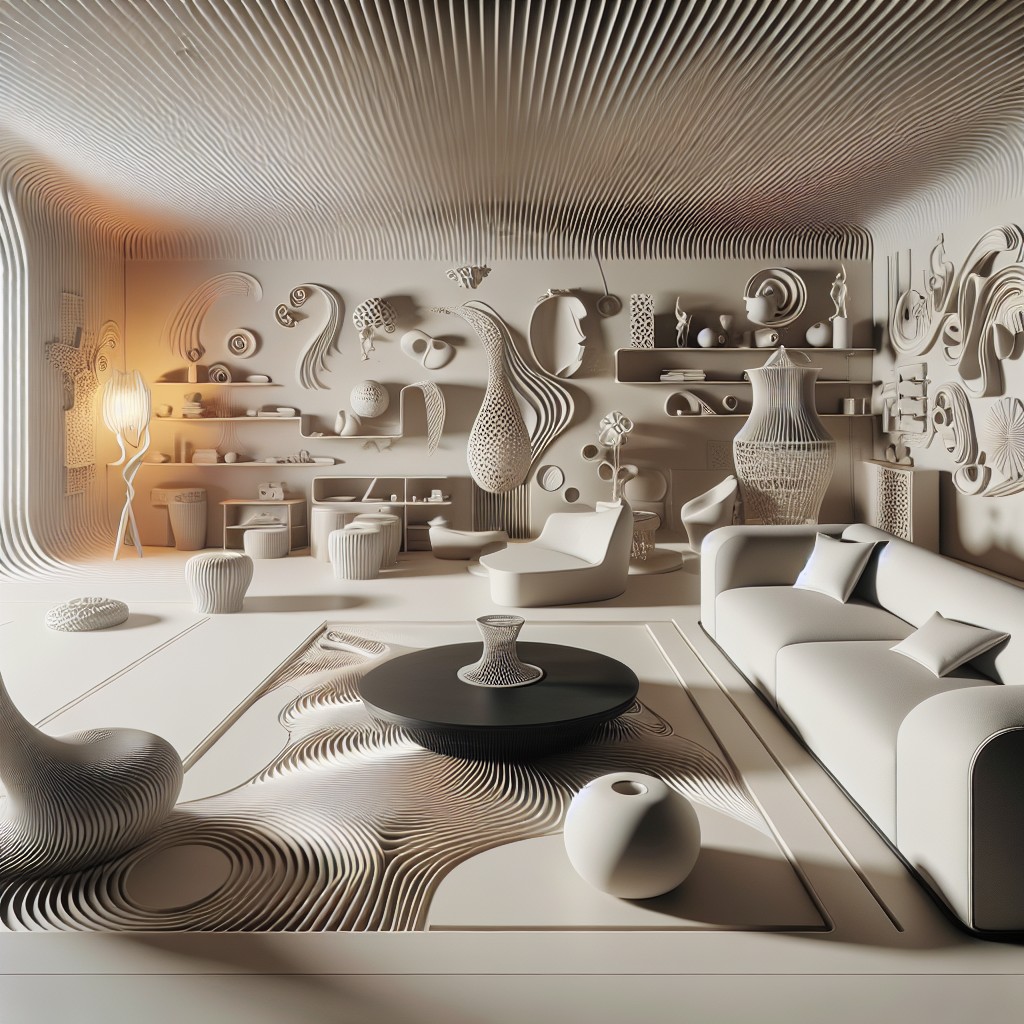
3D printing technology extends beyond the construction of home exteriors, enabling homeowners to create bespoke interior designs that match their living spaces.
Customizable to the smallest detail, these printed furnishings can complement the style and functionality of a 3D-printed house, ensuring a consistent aesthetic and design language throughout.
- Tailored Fit: Items can be designed to fit specific dimensions and layouts, optimizing space and creating a seamless flow within rooms.
- Material Innovation: From recycled plastics to wood-based biocomposites, a range of sustainable materials can be used for printing, offering both eco-friendliness and durability.
- Design Freedom: Infinite design possibilities allow for intricate patterns and shapes that are difficult or expensive to achieve through traditional manufacturing methods.
- On-Demand Manufacturing: Furniture and accessories can be produced on-site, reducing transportation costs and the carbon footprint associated with logistics.
- Waste Reduction: Printing on demand means that only the required amount of material is used, minimizing excess and supporting a circular economy.
- Repair and Modification: Easy repairs or modifications of printed items can be made without replacing the entire piece, extending the life cycle of the product.
Through these points, we grasp how 3D printing technologies are shaping not just the structures we live in but also the way we furnish and personalize our living spaces.
The Pros and Cons of Living in a 3D-Printed House
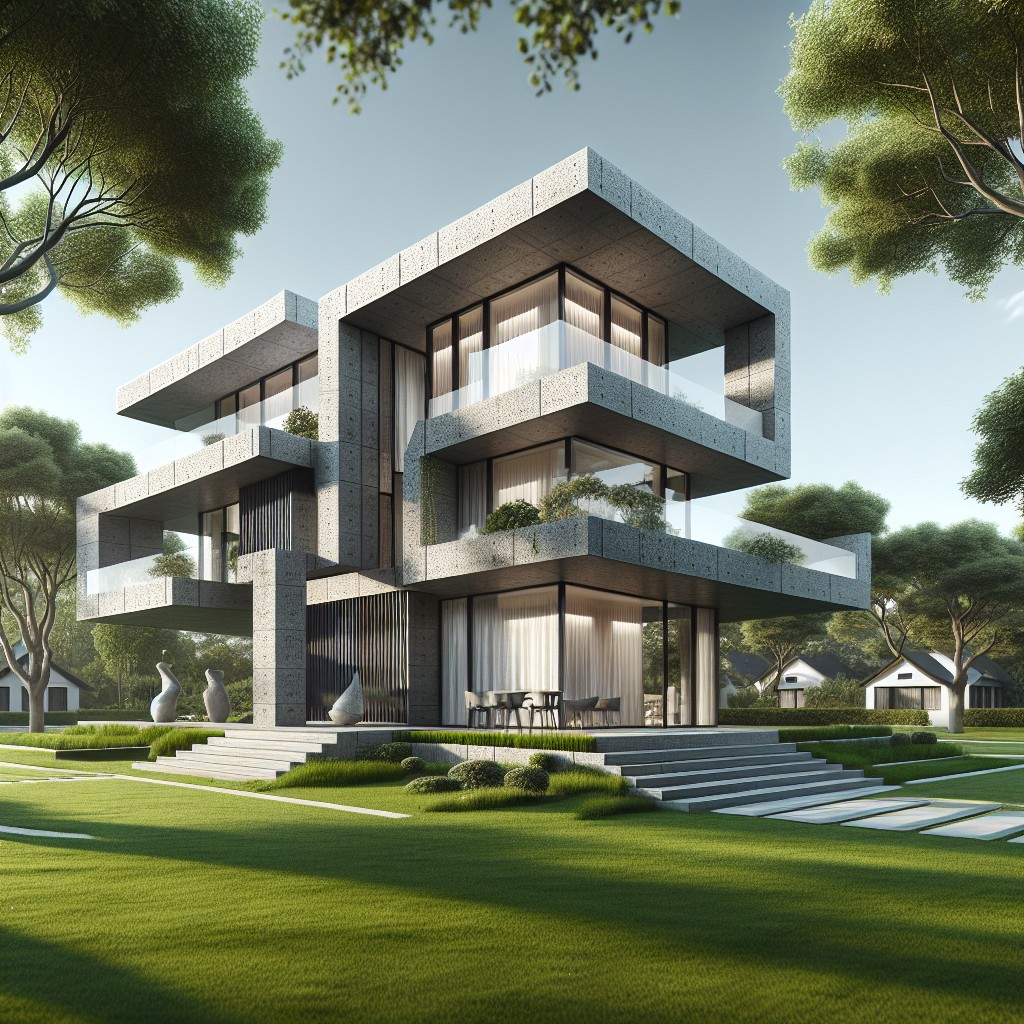
Advantages of 3D-printed homes stem from their innovative construction process. Quick to erect, these houses can be built in a matter of days, significantly reducing labor costs and construction timelines. The precision of 3D printing technology minimizes waste, creating an eco-friendlier building method by using only necessary materials, often recyclable and sourced sustainably.
These homes also offer a high degree of customization. The digital nature of the design process allows for intricate details and complex structures that might be cost-prohibitive or impossible with traditional construction. This opens the door for architectural creativity and individual expression in home design.
On the flip side, the newness of the technology brings potential drawbacks. The limited track record of 3D-printed constructions means long-term durability is not fully understood yet. Regulatory hurdles often follow as building codes and permit processes may not be updated to account for these innovative methods. Additionally, despite a variety of design possibilities, there may be constraints due to the current capabilities of printing equipment and materials that could limit the size and complexity of structures.
Furthermore, while 3D printing promises reduced costs upfront, long-term maintenance costs and the need for special expertise in repairs might offset initial savings. Acceptance can also be a hurdle, as the concept may be too avant-garde for some communities, possibly affecting resale value and market perception.
Disaster Relief: Can 3D Printing Provide Quick Shelter Solutions?
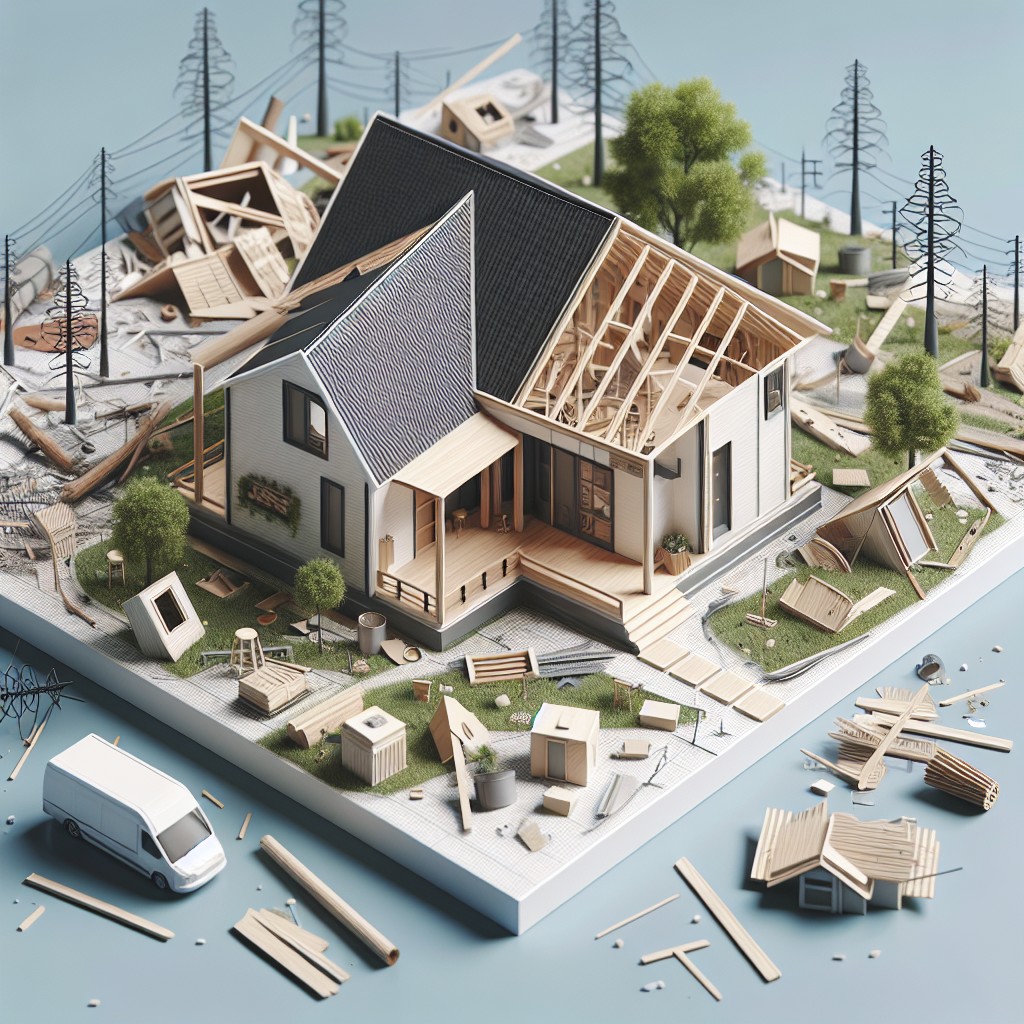
In the wake of a disaster, the need for swift and reliable shelter solutions is paramount. 3D printing rises to this challenge with its rapid construction capabilities. The technology can print habitable structures in a matter of hours, a significant improvement over traditional building methods.
Key points about 3D printing for disaster relief:
- Speed: 3D printers can operate around the clock, drastically reducing build times.
- Efficiency: Less waste is produced compared to conventional construction, making the process more sustainable and cost-effective.
- Versatility: Printers can create designs tailored to specific environmental conditions and available resources.
- Accessibility: Portable 3D printers can be transported to remote or hard-to-reach areas affected by natural calamities.
- Autonomy: With minimal human input needed during the actual construction phase, builders can focus on other urgent tasks related to disaster response.
These attributes make 3D printing an innovative tool in the provision of emergency housing, offering a beacon of hope when rebuilding communities post-disaster.
From Sketch to Reality: 3D Printing Custom-designed Homes
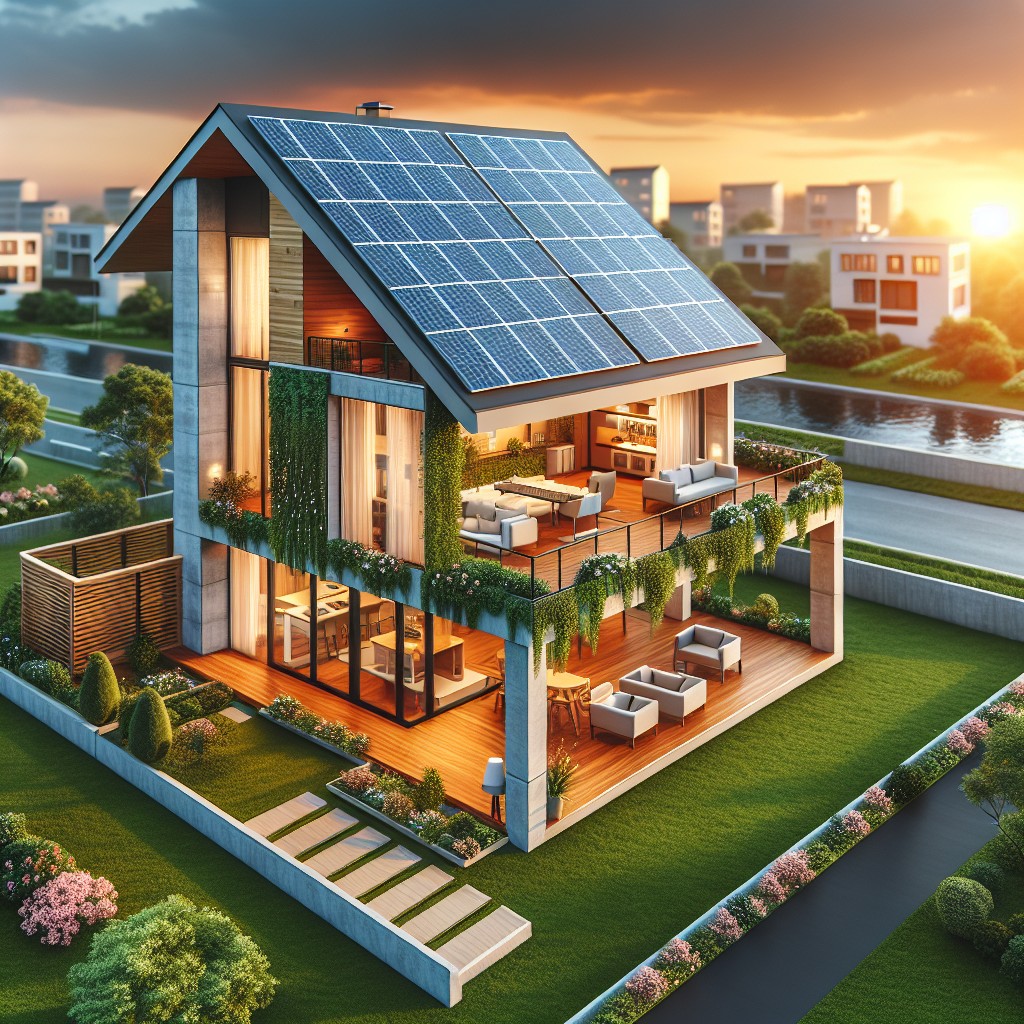
Embracing technology, homeowners can now turn their dream home visions into tangible structures with 3D printing. This process begins often with a simple digital model which is meticulously crafted to meet the client’s desires. The flexibility of design software allows for the customization of every detail, from intricate facades to efficient spatial layouts.
The custom design is then fed into a 3D printer, which deposits materials layer by layer to construct the home. This can include walls with integrated insulation, custom window fittings, and even conduit for electrical wiring. The printers have the unique capability to create curves and angles that might be challenging or costly in traditional construction.
The collaborative aspect of this approach is significant as well. Architects, designers, and homeowners can work together in real-time, making adjustments to the digital model before it is printed. This synergy significantly reduces the margin for error and construction waste, making for a more sustainable building process.
Moreover, the time from conceptualization to completion is drastically reduced. What might take months to build through traditional means could be erected in a matter of days with 3D printing, demonstrating the efficiency and transformative potential of this technology in the realm of bespoke home construction.
3D Printing: A New Era for DIY Home Construction
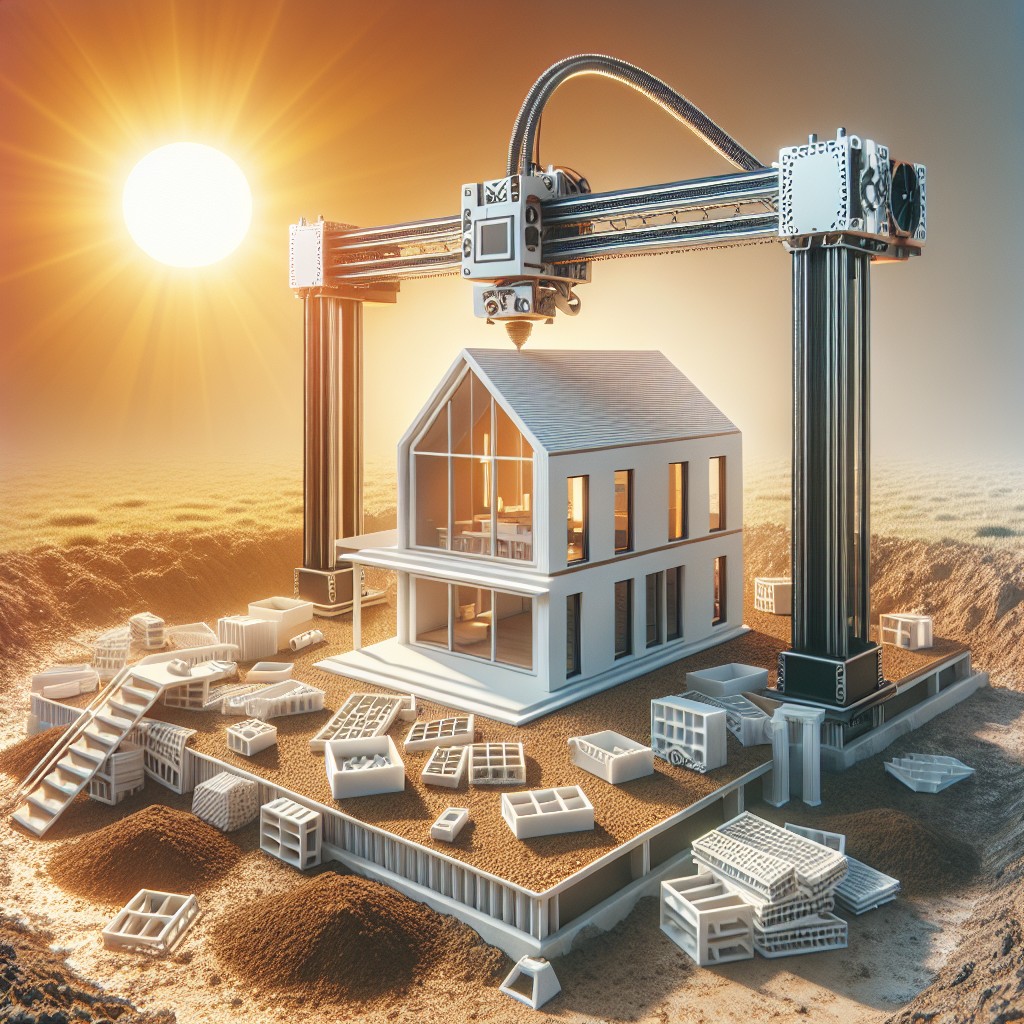
The surge in DIY home construction has seen a remarkable new player: 3D printing technology. This advancement equips individuals with the tools to craft their living spaces with precision and personalization.
- Enhanced Customization: Home builders can adjust designs to their exact specifications, ensuring every inch of the home reflects personal style and functional needs.
- Cost Efficiency: By reducing material waste and leveraging cost-effective building materials, 3D printing makes construction more accessible for budget-conscious builders.
- Time Savings: The rapid assembly capability of 3D printers slashes construction timelines, making it possible to go from foundation to finish in a fraction of the time of traditional methods.
- Accessibility: 3D printing in construction has democratized the building process, making it more accessible to non-professionals without compromising structural integrity.
- Education and Resources: A wealth of online tutorials, courses, and forums now exist to guide DIY builders through the 3D printing process, allowing for a steep learning curve and community support.
By harnessing these points, DIY enthusiasts are not just constructing houses; they’re creating homes, pushing the boundaries of traditional construction and shaping the future of residential building.
How Is 3D Printing Reshaping the Urban Landscape?
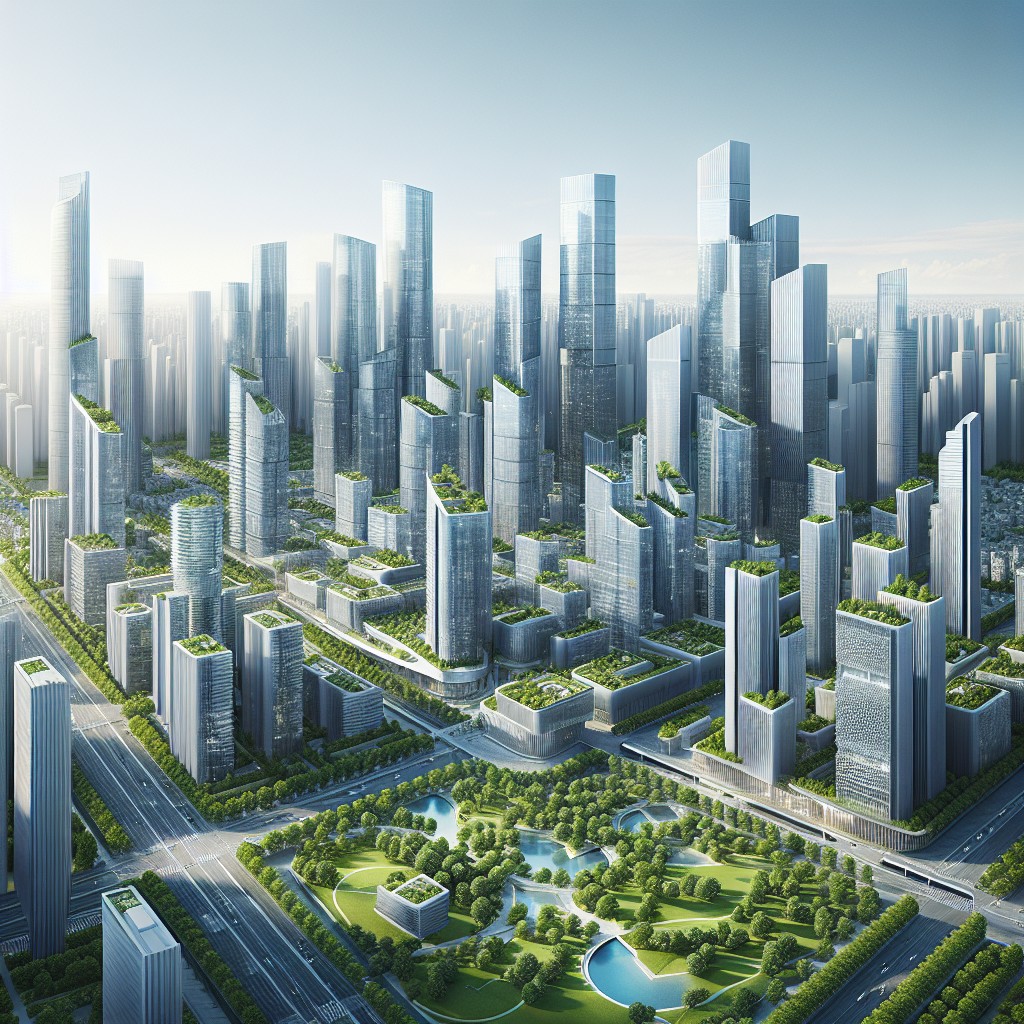
3D printing technology introduces a transformative approach to urban development, offering unique benefits and challenges that reshape cityscapes:
- Speed of Construction: Using additive manufacturing, buildings can be erected significantly faster than traditional methods, minimizing disruption in dense urban environments.
- Design Freedom: The versatility of 3D printing allows for intricate, bespoke designs that can lead to more aesthetically varied and personalized city skylines.
- Cost-Effectiveness: Reducing labor and material waste leads to decreased construction costs, potentially lowering the barrier to entry for developers and encouraging more experimental architecture.
- Sustainability: The precision of 3D printing promotes the use of eco-friendly materials and can contribute to the creation of energy-efficient buildings, aligning with green city initiatives.
- Efficient Land Use: Compact and precise builds tailored to specific site dimensions optimize land use in urban settings, where space is at a premium.
- Community Engagement: The technology can be leveraged for participatory design processes, involving local communities in the shaping of their own neighborhoods, fostering a sense of ownership and inclusion.
These points illustrate the dynamic changes that 3D printing is bringing to urban realms, driving a wave of innovation in how cities grow and evolve.
Incorporating Green Space in 3D Printed Housing Design
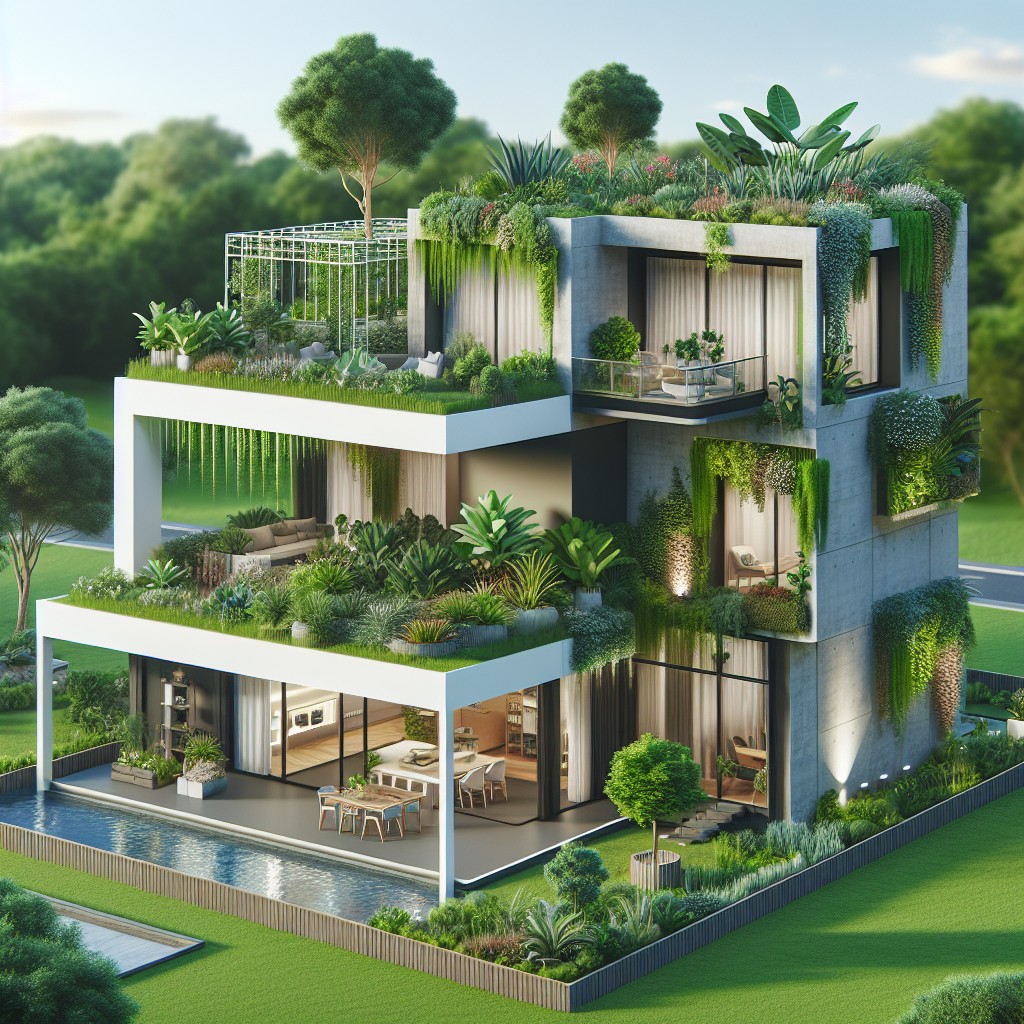
Maximizing natural light and indoor air quality are vital considerations in incorporating green spaces into 3D-printed home designs. Designers can integrate living walls, which improve air quality and bring nature indoors, seamlessly into the structure during the printing process.
Outdoor green spaces enhance the connection with nature and contribute to sustainability efforts. 3D printing allows for the precise design of exterior features such as rooftop gardens, which help in insulation and reducing stormwater runoff, and outdoor planters as part of the home’s structural elements.
Water efficiency is a critical component of sustainable green spaces. 3D-printed homes can include rainwater collection systems in their design that blend with the aesthetics of the house while being highly functional for irrigation purposes.
Solar orientation should be a priority when planning green spaces. Strategic placement of the home and its green space elements can take advantage of the sun’s trajectory for warming in cooler months and shading during hotter periods, reducing energy consumption for temperature control.
Biodiversity can be encouraged directly through architectural design. Habitats for pollinators or native plant gardens not only add beauty but also support local wildlife, fostering a mini-ecosystem within the home’s landscape.
Finally, the use of sustainable, non-toxic materials should be considered for any green space to maintain a healthy environment both indoors and out, while also ensuring the longevity and sustainability of the household ecosystem.
Challenges of Building Code Enforcement for 3D-printed Houses
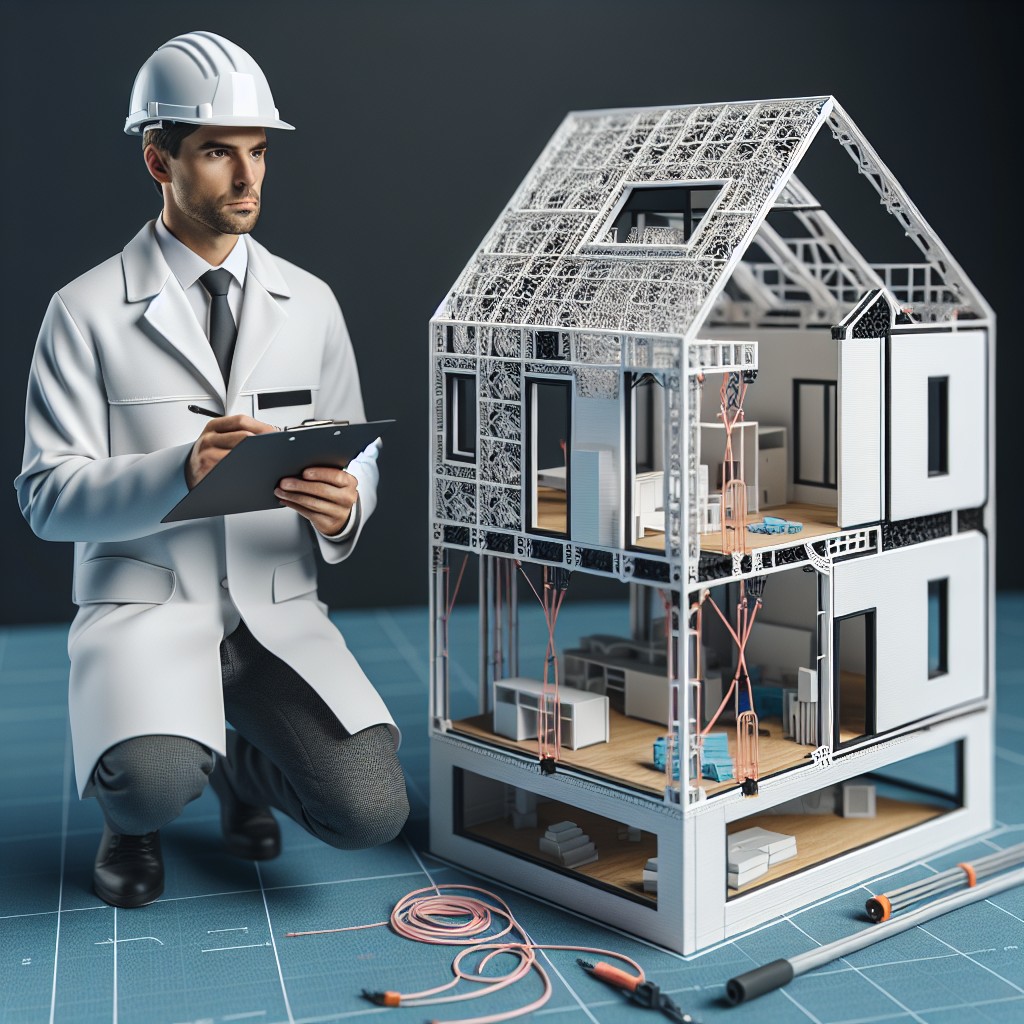
Ensuring that 3D-printed houses meet building codes is one of the major hurdles for widespread adoption. Traditional building codes are designed around conventional construction methods, so adapting them for houses that are printed layer-by-layer presents unique challenges.
Firstly, the consistency of printed materials must be verified for structural integrity. Unlike standard materials, which have established benchmarks, the durability of 3D-printed walls must be rigorously tested to guarantee safety.
Secondly, the novel designs possible with 3D printing often fall outside existing zoning regulations, which can be restrictive in terms of shapes and sizes. Updating these regulations requires collaboration between innovators and regulatory bodies.
Thirdly, the electrical and plumbing systems may need specialized approaches during the printing process to comply with current codes. Integrating these systems into the 3D printing workflow is crucial to ensure functionality without compromising design integrity.
Lastly, as 3D printing technology advances, building codes need regular updates. This demands a proactive and dynamic approach from authorities to keep pace with technological innovations while safeguarding residents.
Addressing these challenges requires open dialogue between 3D printing experts, code officials, and legislators to refine building codes that foster innovation without sacrificing safety and habitability.
The Intersection of 3D Printing and Smart Home Technology
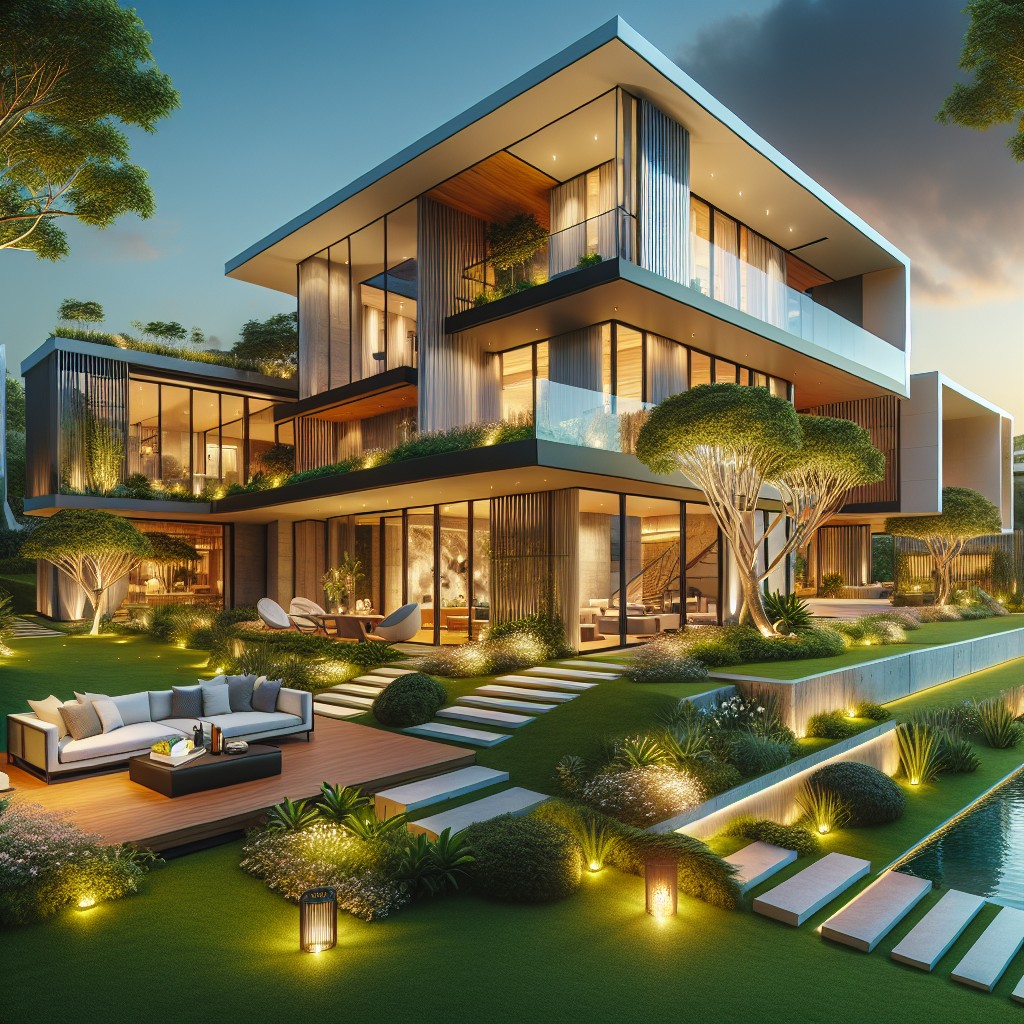
Advancements in 3D printing have converged with smart home technology to create residences that are both futuristic in form and function. Here’s how these two innovative fields blend together:
- Embedded Technology: During the construction phase, 3D printers can embed wiring and sensors within walls, optimizing the integration of smart devices.
- Customization Options: Homeowners can customize the design of their 3D-printed home to include specific mounts and docks for smart devices such as voice assistants, smart lights, and security cameras.
- Material Innovation: The use of conductive materials in 3D printing enables the creation of touch-sensitive surfaces that can be used to control smart home features.
- Energy Efficiency: Smart homes often focus on sustainability. The precision of 3D printing ensures minimal material waste during construction, and designs can be optimized to reduce energy consumption in the finished home.
- Seamless Upgrades: As smart technology evolves, structures printed with modular components allow for easy updates, without the need for intrusive and wasteful construction practices.
- Integrated Systems: Combining smart technology with 3D printing can lead to homes with fully integrated systems for heating, cooling, and ventilation that can be controlled through a single smart home interface.
- Responsive Design: 3D printing enables the creation of designs that actively respond to environmental conditions, working in tandem with smart systems to enhance living comfort and reduce energy use.
By leveraging the versatility of 3D printing with the intelligence of smart home technology, the potential for innovative, personalized, and sustainable living is immense.
Bringing Fairy Tale Houses to Life With 3D Printing
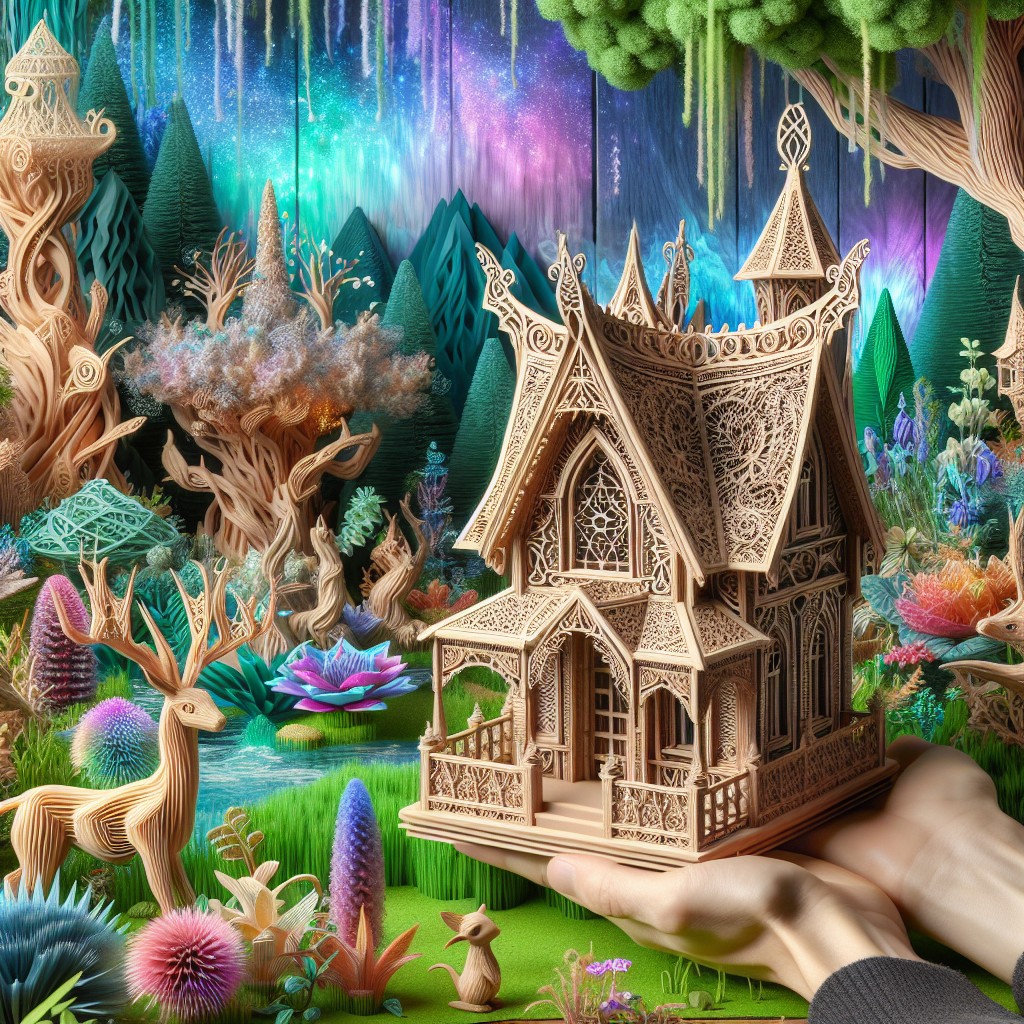
Embracing the charm of storybook cottages or the grandeur of castles, 3D printing taps into the realm of imagination, allowing architects and homeowners to craft homes straight out of a fairy tale. With this innovative technology, the intricate details and whimsical designs that were once exclusive to tales can now be realized in physical form.
- Customization at its peak: Tailoring every nook, turret, and gable to echo centuries-old architecture or fantasy-inspired aesthetics.
- Artistic freedom and precision: Advanced software enables the creation of complex, non-traditional shapes, ensuring precision that traditional construction methods might not achieve.
- Time and resource efficiency: Rapid manufacturing processes reduce lengthy construction timelines and waste associated with traditional building, making it easier to bring these dreamlike structures to life.
- Sustainability in materials: Options for eco-friendly materials mean these enchanting homes can not only look magical but also have a lower environmental impact.
By fusion of traditional architectural elements with the almost limitless possibilities of 3D printing, the creation of personalized, fairy tale-inspired homes is becoming an accessible reality for those looking to turn fantasy into their everyday habitat.
Navigating the Durability and Longevity of 3D-Printed Houses
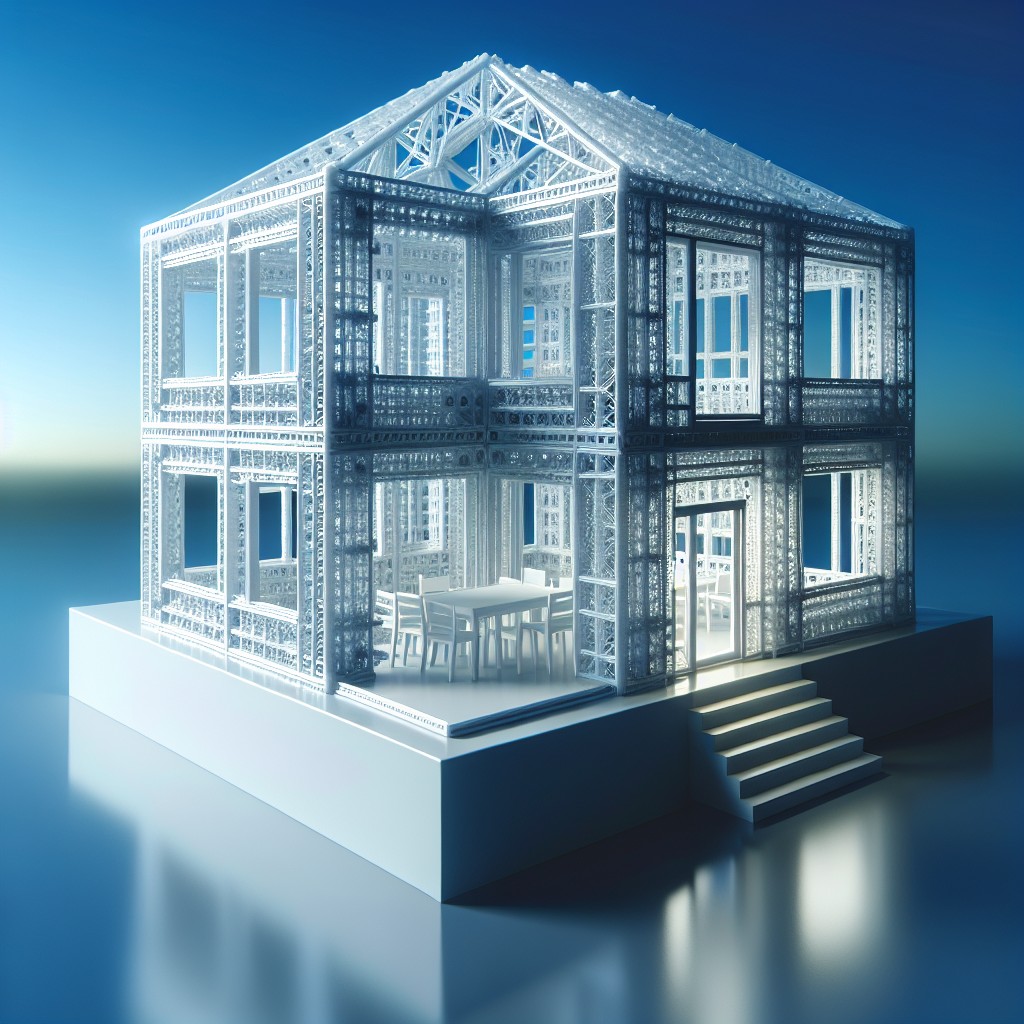
When discussing the robustness of 3D-printed houses, consider these key points:
- Material Matters: The choice of printing material significantly influences durability. Concrete and geopolymers are common for their strength and resistance to elements.
- Design for Longevity: 3D-printing technology allows complex, structurally sound designs that conventional construction might not, which can enhance lifespan.
- Environmental Factors: Homes must withstand local weather conditions. 3D-printed materials are tested for exposure to extreme temperatures, moisture, and other climate-specific stresses.
- Maintenance and Repairs: Just like traditional homes, regular maintenance ensures longevity. The ease of repairing 3D-printed components can contribute to a longer-lasting structure.
- Technological Advancements: Continuous improvements in 3D printing technology and materials research are extending the potential lifespan of these homes.
- Real-Life Performance: Case studies and ongoing monitoring of existing 3D-printed homes provide valuable data on their actual aging process and long-term performance.
Understanding these aspects will give you insight into the sustainability and practicality of choosing a 3D-printed home.
Overcoming Homelessness With 3D-Printed Housing Solutions
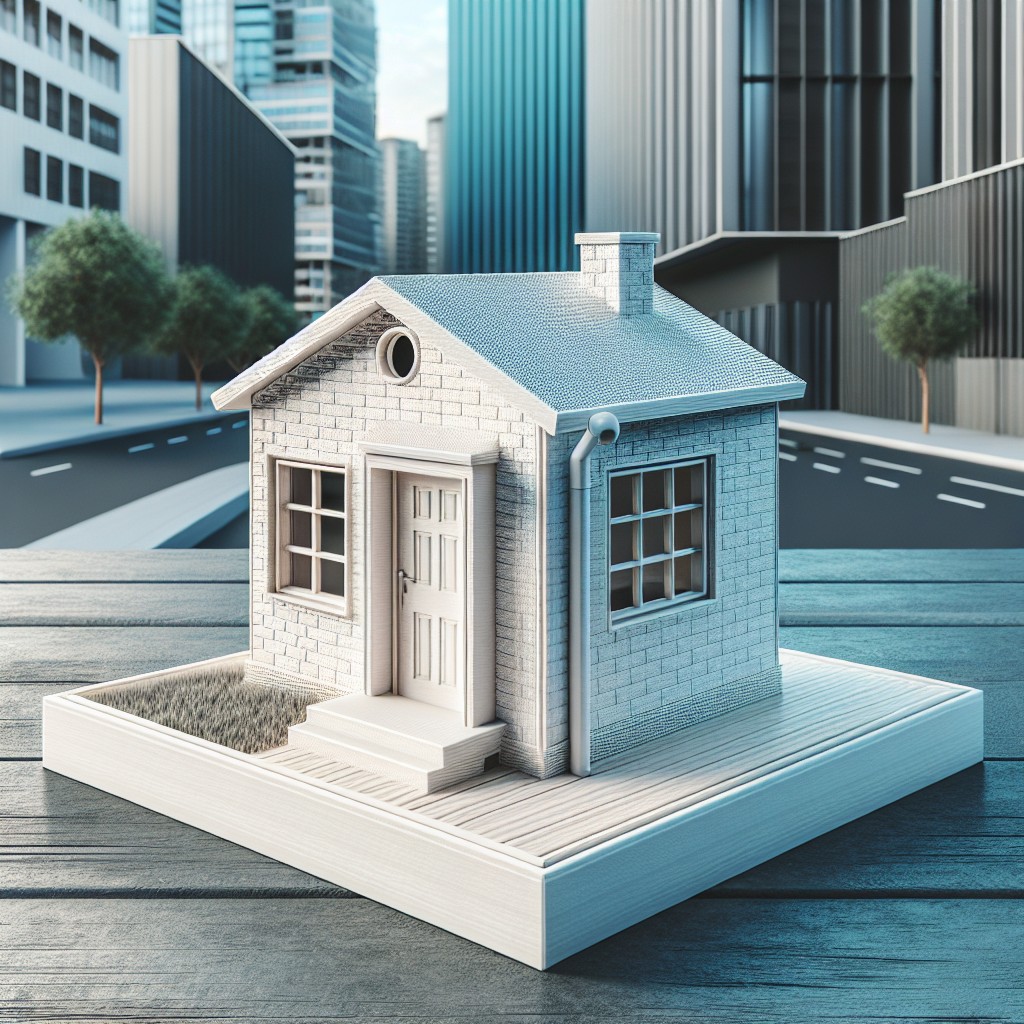
3D printing presents an innovative approach to reducing homelessness by creating cost-effective, rapidly-built homes. This technology reduces labor costs and material waste, directly translating into more affordable housing options.
Quick Construction: Homes can be printed in a matter of days, providing immediate shelter for those in need.
Resource Efficiency: By using precise amounts of building materials, 3D printing minimizes waste, contributing to both environmental sustainability and reduced construction costs.
Customizable Designs: Through 3D printing, homes can be tailored to fit the needs of individuals and families, promoting a sense of dignity and comfort.
Scalability: The technology is scalable, allowing for the production of single homes or entire communities depending on the demand, making it a viable solution for both small-scale and larger homeless populations.
Local Material Use: Many 3D printers can use locally sourced materials, further reducing costs and fostering local economies.
Community involvement and government initiatives can amplify the benefits of this solution, helping integrate these houses into city planning and social services. By partnering with private companies, non-profits, and local communities, this innovative method is transforming the fight against homelessness.
Building Multi-story Buildings: The Next Level in 3D-Printed Houses

As 3D printing technology advances, architects and engineers are exploring the vertical potential of construction. The ability to build upwards is crucial for urban areas where space is at a premium. Traditionally, constructing multi-story buildings involves complex formwork, scaffolding, and a range of materials. With 3D printing, however, the process becomes streamlined and efficient.
Key points to understand about multi-story 3D-printed buildings include:
- Structural Integrity: Unlike single-story structures, multi-story designs demand careful considerations for load-bearing walls and wind forces. Printed materials must provide sufficient strength and stability as the height increases.
- Printing Techniques: The process typically requires printing sections or modules on-site or off-site, which are then assembled layer by layer to create the full structure.
- Material Innovation: To ensure safety and durability, research continues into specialized concrete mixes and composite materials optimized for both printing precision and structural resilience.
- Design Flexibility: With 3D printing, complex architectural features can be created without significantly increasing costs, offering architects the freedom to innovate.
- Sustainability: Building upwards reduces the building’s footprint and can contribute to better land use. Additionally, 3D printing minimizes waste as it uses only the necessary amount of material.
- Time Efficiency: The construction timeline is shortened since 3D printing can operate continuously and doesn’t require traditional curing times between layers.
Engineers and designers must work in close collaboration to address challenges such as ensuring seamless connections between floors and optimizing the layout for both comfort and safety. With these considerations in mind, multi-story 3D-printed buildings are moving from concept to reality, paving the way for a new era in construction.
Exploring Commercial Use of 3D Printing for Hotel and Resorts
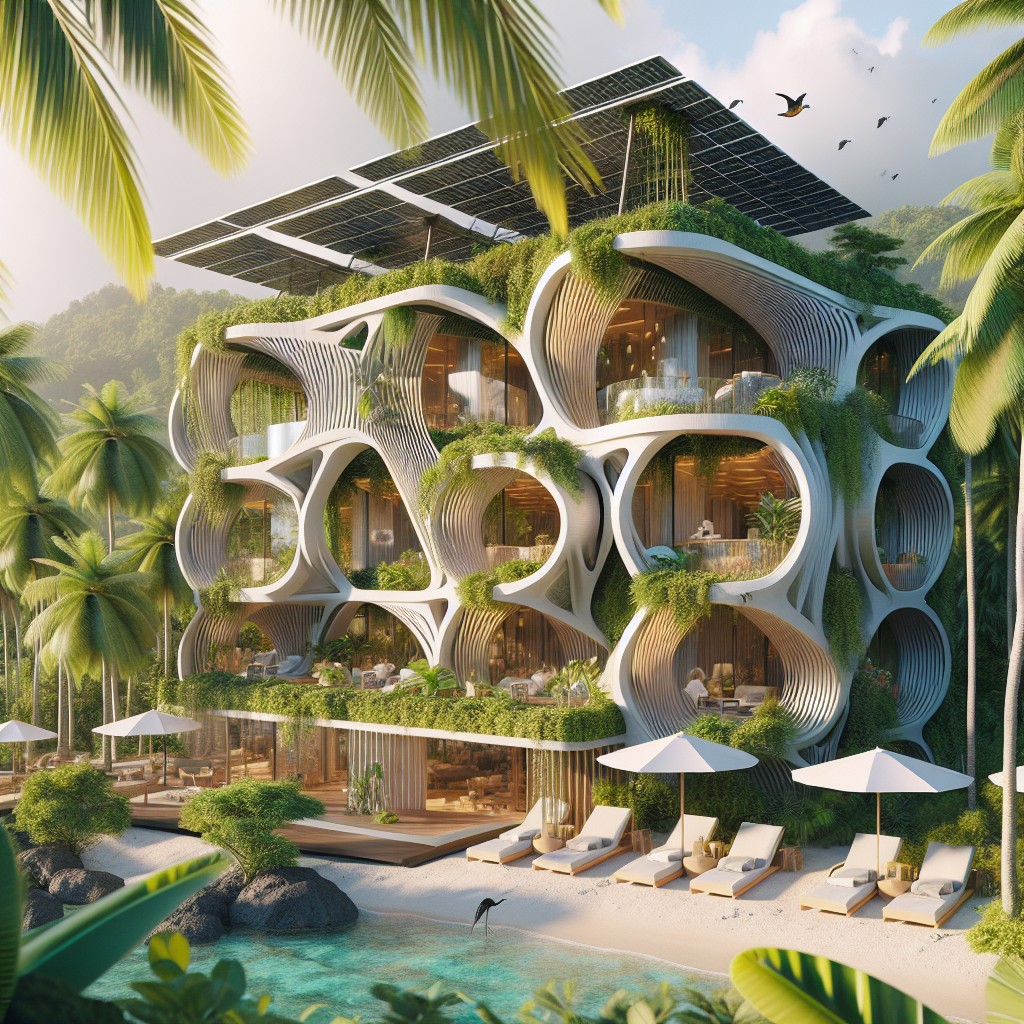
Harnessing 3D printing for hotels and resorts unlocks several enticing possibilities. With rapid construction speed, hoteliers can reduce build times significantly, allowing them to respond swiftly to market demands or tourism trends. This technology also paves the way for unique architectural designs previously constrained by traditional building methods, essentially enabling structures to become landmarks in their own right.
Sustainability is at the forefront of this innovation. 3D-printed hotels can integrate eco-friendly materials that minimize environmental impact. The precision of 3D printers ensures material usage is optimized, slashing waste during construction. Additionally, the ability to print complex designs can incorporate natural cooling systems or solar collection capabilities directly into the structure’s walls, bolstering energy efficiency.
In locations remote or difficult to access, transporting building materials and machinery is costly and challenging. 3D printing presents a solution: mobile printers can be set up on-site, utilizing local materials, and overcoming logistical hurdles. This accessibility inversely impacts the local economies, creating jobs, and engaging the community in the construction process.
Customization is another area where 3D printing shines. Tailoring individual rooms or suites to specific themes or luxury standards becomes more feasible, offering guests a unique, personalized experience that can adapt and evolve with guest feedback and design innovation.
Finally, maintenance and repairs can be more efficient. Having digital blueprints on file allows for the exact replication of elements of the hotel or resort, aiding in consistent quality and brand standards across multiple locations. This digital advantage transforms how hospitality businesses maintain their properties over time.
Fusing 3D Printing and Traditional Home Building Techniques
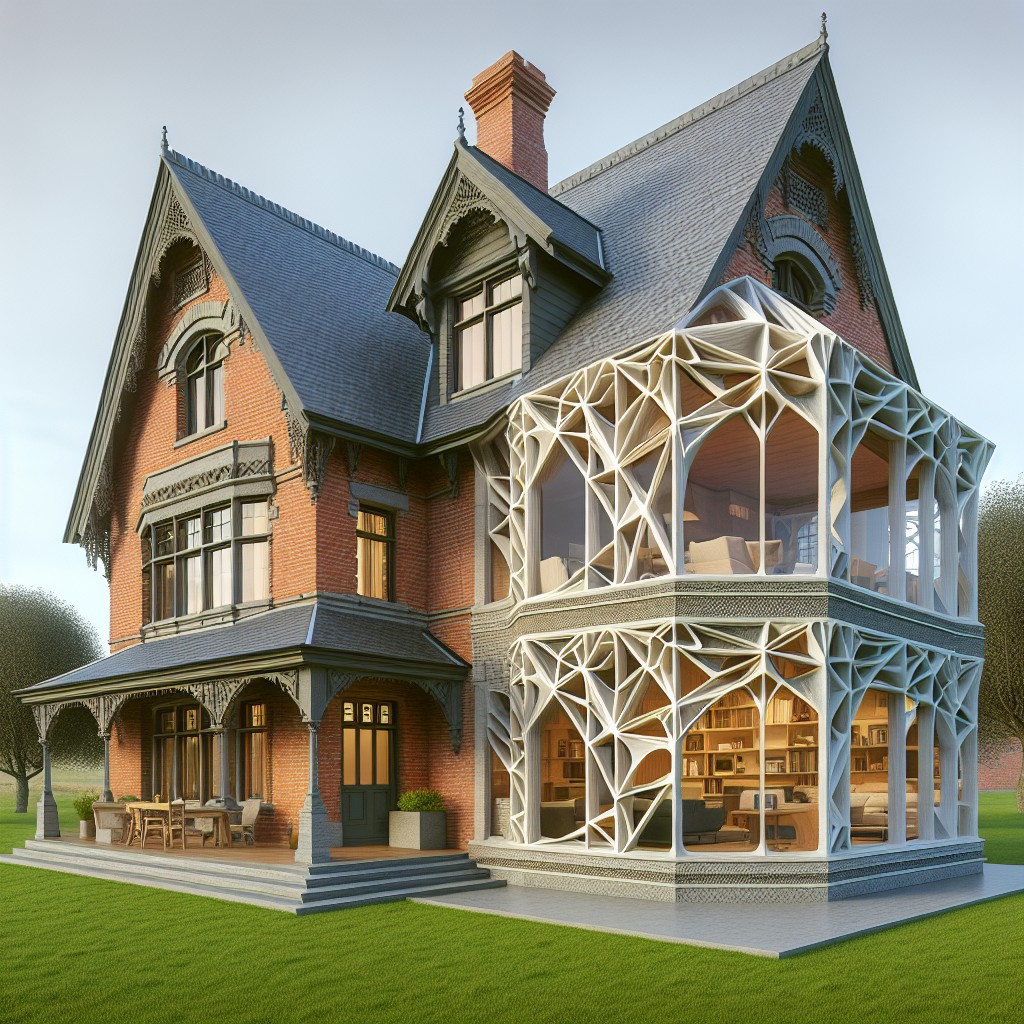
Combining 3D printing with conventional construction methods offers a balanced approach that capitalizes on the strengths of both techniques. Here’s how these methodologies come together to enhance home building:
- Structural Integrity: Traditional materials like wood and steel provide a robust framework, while 3D printing fills in the gaps, creating complex geometric shapes that might be difficult or expensive to achieve otherwise.
- Customization and Detailing: Craftsmanship from standard practices can merge with the precision of 3D printing, allowing intricate designs and personalized details, from unique facade elements to bespoke interior finishes.
- Cost and Time Efficiency: For parts of the build that require speed and lower cost, 3D printing takes the lead. Then, skilled labor is applied where the human touch is irreplaceable, balancing overall project expenses and timelines.
- Sustainability: 3D-printed components can be optimized for resource efficiency, working alongside locally-sourced traditional materials to minimize the environmental impact.
- Compliance and Safety: 3D printing provides exacting standards for parts of the construction, while traditional methods ensure compliance with local building codes and regulations, especially for structural elements.
By smartly integrating these building approaches, homes not only benefit from the revolutionary speed and design versatility of 3D printing but also maintain the time-tested quality and reliability of tried-and-true construction methods.
Implementing 3D Printing in Renovating and Retrofitting Old Buildings
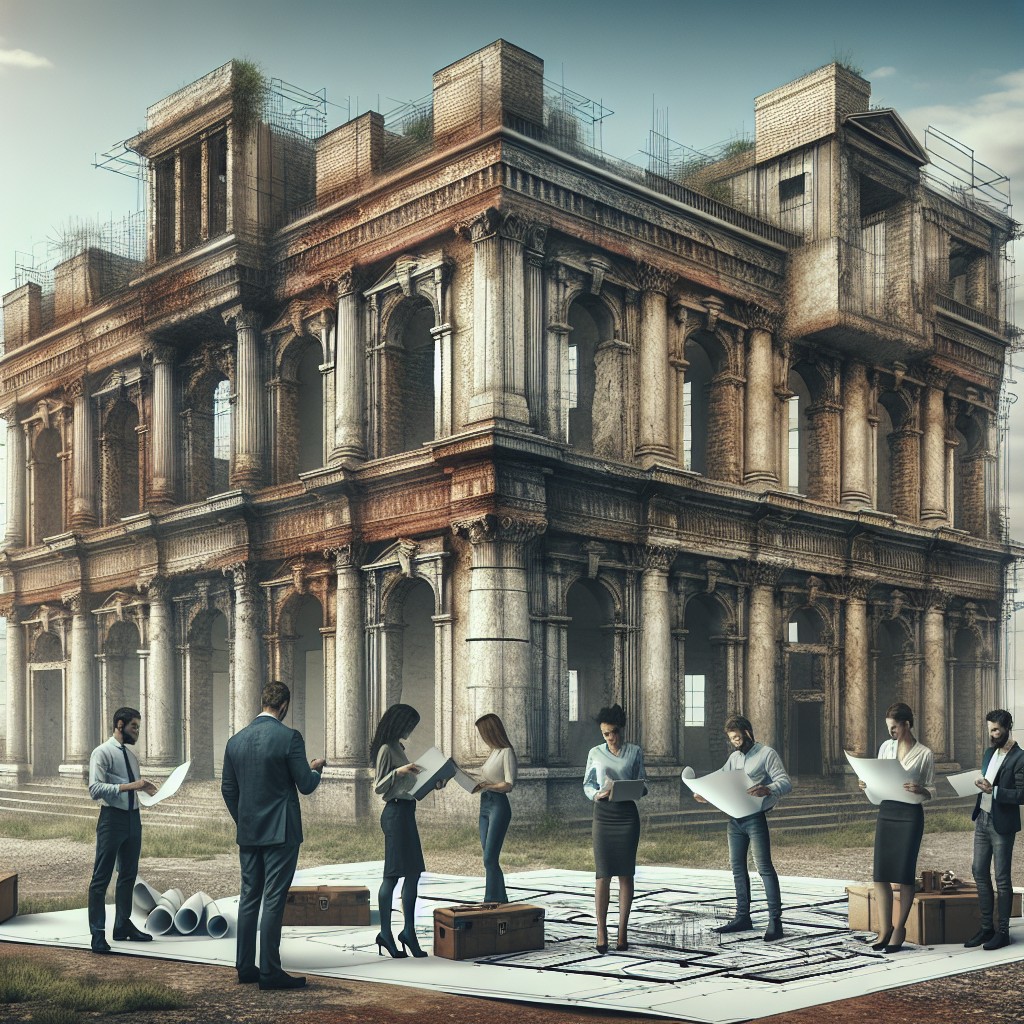
3D printing offers a novel approach to the renovation and retrofitting of existing structures:
- Preserving Historical Integrity: Custom-printed components can replicate ornate details of historical buildings, matching the original materials in appearance but potentially offering improved durability and sustainability.
- Energy Efficiency Upgrades: Insulation and other elements designed to improve a building’s energy efficiency can be 3D printed to fit perfectly within existing walls and frameworks, minimizing disruption and waste during the installation process.
- Structural Reinforcement: For buildings requiring additional support, 3D printing can produce tailored reinforcements that seamlessly integrate with the existing architecture, strengthening the building without the need for extensive alterations.
- Cost-Effective Customization: By 3D printing specific parts needed for retrofitting, costs can be reduced as there is less need for bespoke craftsmanship and materials can be optimized for their purpose, leading to less waste.
- Rapid Prototyping: Before implementing changes, 3D printing allows for rapid prototyping of design modifications, enabling stakeholders to evaluate potential renovations and ensure compatibility with the original structure.
- Accessibility Features: With an aging population, there’s an increasing need for accessibility in historic homes. 3D printing can create bespoke ramps, rails, and other features that are sympathetic to the building’s design while enhancing accessibility.
By integrating 3D printing into the renovation process, the blend of old and new can be done smoothly while maintaining the character and longevity of the building.
Ideas Elsewhere
- https://builtin.com/3d-printing/3d-printed-house
- https://cobod.com/explore-designs-and-interiors-of-3d-printed-houses/
- https://www.reddit.com/r/engineering/comments/qh4ik2/3d_printed_houses/
- https://designwanted.com/3d-printed-houses/
- https://www.reddit.com/r/3Dprinting/comments/16rw3hm/inprogress_3d_printed_house_in_nw_houston_see/
- https://all3dp.com/2/3d-printed-house-3d-printed-building/
Table of Contents